
来源 | 封装工艺精进
智库 | 云脑智库(CloudBrain-TT)
云圈 | 进“云脑智库微信群”,请加微信:15881101905,备注研究方向
Chapter 3 Fan-in Wafer-Level Packaging Versus FOWLP
3.1 Introduction
扇入式晶圆级封装(WLP)技术[1-19]将在本章中进行讨论。将设计和制造晶圆级芯片规模封装(WLCSP),然后将其组装在印刷电路板(PCB)上。重点放在使WLCSP的重新分布层(RDL)及其PCB焊点可靠性上的关键工艺步骤上。 与大多数焊点可靠性研究不同,后者要生成足够的测试数据以拟合寿命分布[20-28],本研究的目标之一是确定WLCSP焊点中的裂纹萌生和裂纹扩展。在PCB组件上。 在热循环过程中,WLCSP焊点中的裂纹如何增长(传播)?这是一个常见问题,答案可能对设计WLCSP焊点的可靠性很有用。 在这项研究中,WLCSP焊点的裂纹长度是根据热循环次数进行测量的,即通过实验确定WLCSP焊点的疲劳裂纹增长率。提出了使用裂纹尖端断裂特性来预测WLCSP焊点热疲劳寿命的经验方程式,如本节中所示。 3.10(假设焊料是一种弹性材料)的应力强度因子KI(打开模式)和KII(剪切模式),见第6节。 3.10(假定焊料是一种弹塑性材料),用于J积分,如S节中所示。 平均蠕变应变能密度为3.10(假设焊料为蠕变材料)。 由于管芯退缩,在管芯上增加更多功能以及系统级封装(SiP)的普及,扇入WLP正面临着扇出晶圆级封装(FOWLP)的激烈竞争[29–53], 将在第4、5、6、7、8、9和11章中讨论。
3.2 Fan-in Wafer-Level Packaging (WLP)
在过去的18年中,扇入式WLP已广泛用于移动,便携式和消费类产品中。特别是,它用于容纳低引脚数(200),小裸片尺寸(6 mm 6 mm),低成本,低端,低轮廓和大批量应用的半导体器件。3.3 Wafer-Level Chip Scale Packages(WLCSPs)
采用扇入式晶圆级封装技术制成的封装称为晶圆级芯片级封装(WLCSP)[1-19]。 大多数WLCSP的独特功能是使用金属(通常是Cu)RDL将晶片上的细间距外围排列的焊盘重新分布到具有更高焊锡凸点的更大间距区域排列的焊盘上,如图5和6所示,3.1和3.2。因此,有了WLCSP,就可以减轻对PCB的需求,并且可能不需要进行填充。从系统制造商的角度来看,WLCSP就像另一个“焊锡芯片”表面安装组件一样,除了以下几点:(a)WLCSP的焊料凸点越来越高; (b)WLCSP的PCB组件更坚固; (c)他们非常高兴,以至于不必与填充不足的密封剂作斗争。3.4 WLCSP Test Vehicle
设计并制造了WLCSP测试项目,然后将其组装在PCB上以证明其可行性和可靠性[2]。3.4.1 The Chip
图3.1显示了正在考虑的晶片上的硅芯片。该芯片为6.5毫米6.5毫米0.5毫米,在两个相对的侧面上有48个焊盘(节距为0.2毫米)。3.4.2 The WLCSP
通过在晶圆顶部添加额外的金属层,可以将芯片上的细间距外围阵列焊盘重新分布到芯片内部更大的间距和面积阵列焊盘上。在这种情况下,在晶圆级重新分配后,新的焊盘(直径0.33毫米)采用间距为0.75毫米的区域排列格式。WLCSP由铜导体层(RDL)和两个低成本的聚酰亚胺介电层组成。图3.2显示了重新分配的详细信息。可以看出,焊料凸点由铜芯支撑,该铜芯通过凸块下凸铜冶金(UBM)连接到重新分布的Cu-Ni焊盘。重新分布的金属层由Cu-Ni制成。3.4.3 WLCSP Key Process Steps
以下简要讨论了WLCSP的关键流程步骤(图3.1和3.2)。首先,对晶片进行超声波清洗。 •步骤1:在晶片上旋转聚合物,例如聚酰亚胺(PI),苯并环丁烯(BCB)或聚苯并-双恶唑(PBO),并固化1小时。这将形成一个4-7lm厚的层。 •步骤2:施加光刻胶和掩模,然后使用光刻技术(对准和曝光)在PI,BCB或PBO的顶部打开通孔。 •步骤3:蚀刻PI,BCB或PBO。 •步骤4:剥离光刻胶。 •步骤5:在整个晶片上溅射Ti和Cu。 •步骤6:施加光刻胶和掩模,然后使用光刻技术打开重新分布轨迹的位置。 •步骤7:在光刻胶开口中电镀Cu。 •步骤8:电镀镍。 •步骤9:剥离光刻胶。 •步骤10:蚀刻掉Ti / Cu。 •步骤11:与步骤1相同(对于UBM)。 •步骤12:应用光刻胶和掩模,然后使用光刻技术在光刻胶上打开所需凸块焊盘的过孔,并覆盖重新分布的走线。 •步骤13:蚀刻PI,BCB或PBO。 •步骤14:剥离光刻胶。 •步骤15:在整个晶片上溅射Ti和Cu。 •步骤16:施加光刻胶和掩模,然后使用光刻技术打开凸块焊盘上的通孔,以使用UBM露出区域。 •步骤17:电镀铜芯。 •步骤18:电镀焊料。 •步骤19:剥离光刻胶。 •步骤20:蚀刻掉Ti / Cu。 •步骤21:施加助焊剂并回流63Sn37Pb焊料。 WLCSP凸块的典型横截面如图3.2所示。测量了WLCSP的焊料凸点高度和Cu芯高度,结果如图3.3所示。可以看出,铜芯高度和焊料凸点高度都非常统一。在本章中,芯片上的焊料在连接到PCB之前被称为焊料凸点。在将焊料凸块回流到PCB上后,它们被称为焊点。 WLCSP的焊料凸点在以下条件下进行剪切测试[20]:(1)剪切刀片的速度为100 µm/ s,(2)剪切刀片的尖端距离芯片表面100 µm。结果如图3.4所示。可以看出,平均焊料凸点剪切力为404 gf,比传统的倒装芯片焊料凸点的剪切力(50 gf)高出许多倍。注意,故障位置在焊料凸块上(不在UBM处),并且断裂表面以剪切为主,图3.5。3.5 PCB Assembly of the WLCSP
将WLCSP组装在0.52毫米厚的FR-4 PCB上非常容易。将焊锡凸出的WLCSP与带有查找和查找照相机的PCB对准后,将免清洗助焊剂施加到PCB上,最后以最小的力将WLCSP面朝下放在PCB上。放置WLCSP后,将其放在回流炉的传送带上,最高PCB温度为235°C(图3.6)。由于大量的焊料和回流焊过程中的表面张力,因此组装过程非常坚固。典型的横截面WLCSP-PCB组件如图3.7所示,清楚地展示了独特的凸焊WLCSP自对准特性。同样,它清楚地表明,正确完成了Cu / Ni RDL,Ti / Cu势垒/种子层和PI。3.6 Thermal Cycling Test of WLCSP-PCBAssembly
3.6.1 Thermal Cycling Condition
PCB组件上的WLCSP经过热循环测试。施加在组件上的温度负载如图3.8所示。可以看出,对于每个循环(60分钟),温度在-20至+110°C之间,斜升15分钟,高温保持20分钟,而低温保持10分钟。选择此温度曲线的原因有两个:(1)FR-4 PCB的玻璃化转变温度为120°C,并且由于PCB的退化,我们不想引入焊点的其他失效机制; (2)-20°C以下的焊料行为不是很清楚。
3.6.2 Crack Length Distribution of AllSolder Joints
由于焊点到中性点(DNP)的距离不同,因此所有焊点的裂纹长度都可能不同。通常,焊点具有最大的DNP,这将导致最大的裂纹长度。图3.9显示了在2400个循环时焊点中裂纹长度的映射。实际上,第一行焊点(1、9、17、25、33和41)的外部裂纹长度大于第二行和第三行焊点的外部裂纹长度。同样,角焊点的裂纹长度最大。
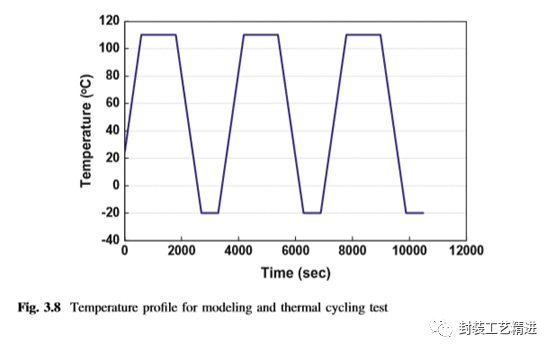
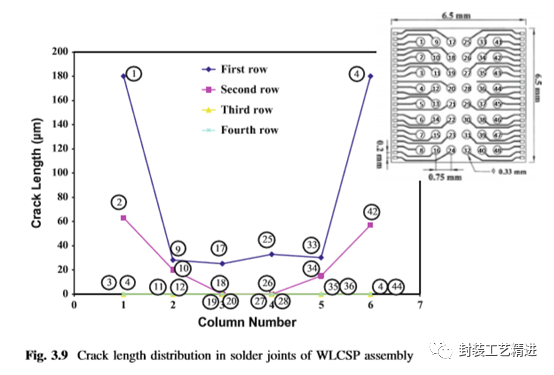
3.6.3 Crack Propagation of the CornerSolder Joint
应该指出的是,与大多数焊点可靠性研究不同,后者要生成足够的测试数据以拟合寿命分布[20-28],本研究的目标之一是确定裂纹的产生和扩展。在PCB组件上的WLCSP的焊点中。裂纹在任何结构中的产生和传播一直是非常复杂的现象。初始裂纹长度和裂纹扩展长度也很难定义。在本研究中,在100、200、500、800、1000、1200、1500、2000和2400个循环下,从热循环室中取出三个WLCSP-PCB组件进行检查。在高倍显微镜下检查横截面样品的裂纹。重要结果总结如下[2,14-18]:(1)直到800次循环,焊点都没有明显的裂纹(图3.10a和b)。应该指出的是,由于样品量少(3)和显微镜的作用,可能会在更早的时候出现一些很小的细小裂纹。
(2)在800至1000次循环之间,角焊点的两侧均出现裂纹。内部裂纹长度(朝向切屑中心)= 25 lm,外部裂纹长度= 40 lm,图3.10b。外裂纹首先开始,如图3.11b所示。
(3)在1000到1200个循环之间,内部裂纹长度扩展到37 lm,而外部裂纹长度扩展到48 lm,如图2和图3所示。 3.10c和3.11c。
(4)在1200至1500个循环之间,内部裂纹长度= 70 lm,外部裂纹长度= 100 lm,图3.10d。 (5)在1500和2000个循环之间,内部裂纹长度增长到100 lm,外部裂纹长度增长到140 lm,图3.10e。
(6)在2000至2400次循环之间,裂纹将角焊点分开。 3.10f和3.11d。
(7)在角焊点中,裂纹在PCB的铜焊盘附近引发并扩展。
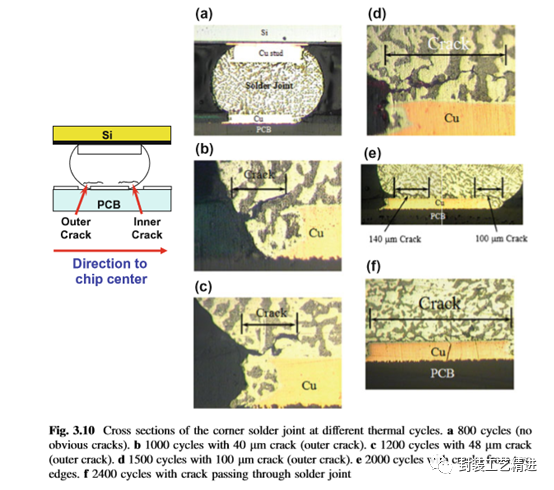
3.6.4 Fatigue Crack Growth Rate
图3.12显示了角焊点的内部和外部裂纹长度与热循环次数的关系。可以将它们曲线拟合,如图3.13所示,形式如下:其中a是裂纹长度,N是循环数,C1和C2在表3.1中给出。因此,对于角焊点,外部和内部裂纹的长度可以通过公式确定。 (3.2)对于给定数量的热循环。另外,角焊点的疲劳裂纹扩展率(da / dN)可以由式(1)求出。 (3.5)。3.7 Fracture Characteristics of the Corner Solder Joint—Solder Material and Properties
焊点由63Sn–37Pb焊料制成,泊松比为0.4,热膨胀系数(CTE)为2110-6 /°C。焊料的杨氏模量(图3.14)和应力-应变关系(图3.15)与温度有关。铜(Cu)的杨氏模量,泊松比和CTE分别为76 GPa,0.34和17 10-6 /°C。FR-4 PCB的CTE为18.5 10-6/°C,Si WLCSP的CTE为2.5 10-6 /°C。计算建模中使用的材料属性如表3.2所示。 Garofalo-Arrhenius稳态蠕变通常表示为
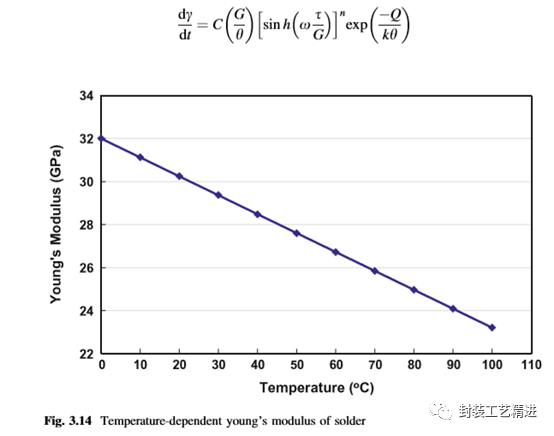
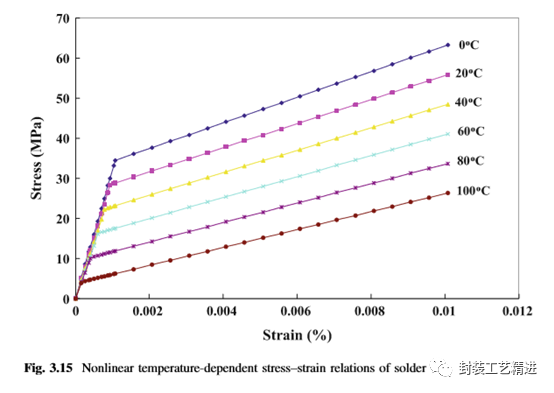
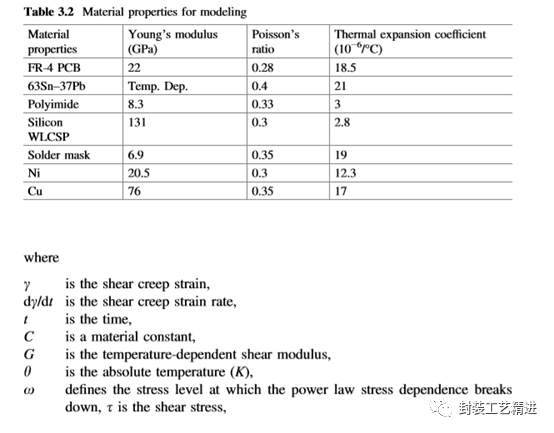
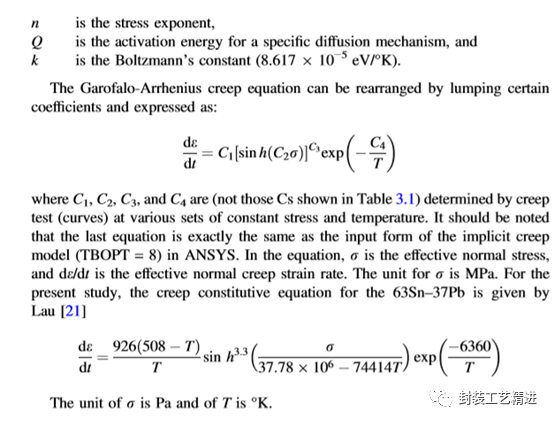
3.8 Fracture Characteristics of the Corner Solder Joint—Geometry
即使角焊点的外部裂纹和内部裂纹(朝芯片中心)的引发和扩展并不完全相同,但是,为了简化建模,它们被假定为相等。图3.16显示了用于断裂力学有限元建模的角焊点。可以看出,焊点的高度为0.24mm,底面和顶面的直径分别为0.28和0.3mm。由于Si WLCSP和FR-4 PCB之间PCB组件上的WLCSP全局热膨胀不匹配(3.2259 130 [18.5-2.5] 10-6 = 0.0067 mm),以及角焊点的热膨胀, 在热循环条件下,焊点承受着复杂的应力和应变状态。这些应力和应变产生了导致焊点失效的驱动力。由于诸如焊料之类的易延展材料的大部分热疲劳寿命都用于传播裂纹(即疲劳裂纹扩展),因此裂纹尖端周围的应力和应变(应力强度因子,J积分或蠕变应变能量密度) 焊缝中不同裂纹长度的变化非常重要。3.9 Fracture Characteristics of the Corner Solder Joint— Elastic Thermal Fatigue Life Prediction Model (DK)
3.9.1 Boundary Value Problem
在本研究中[14],假设焊料(63Sn–37Pb)是一种弹性材料,并且考虑了五个不同的裂纹长度。这些裂纹对称地位于PCB上的铜焊盘上方10 lm处。在这项研究中使用了八节点的平面应变单元,单位是牛顿和毫米。在裂纹尖端,将中侧节点放置在四分之一点处,以捕获应力中的奇异性。由于诸如焊料之类的易延展材料的大部分热疲劳寿命都用于扩展裂纹(即疲劳裂纹的增长),因此应力和应变焊缝中不同裂纹长度的裂纹尖端周围的应力强度因子(应力强度因子)是最重要的。角焊点上施加的边界条件如图3.16所示,其中固定了底面,使焊点的顶面(节点)发生了0.0067 mm的位移,对整个焊点进行了校正。温度变化130°C。通过指定垂直位移到那些节点的节点耦合,也可以限制顶面旋转,以使垂直位移相同。在规定的载荷下,图3.16中的左裂纹有望弹出,而右裂纹应保持闭合。代替使用接触元件,节点联接器可方便地用于模拟右裂纹表面的闭合和滑动。在ANSYS(商业有限元代码)中,右裂纹表面上的节点在重合节点处沿垂直方向结点耦合,而在水平方向上自由滑动。通过使用节点联接,当裂纹闭合时,裂纹表面不会穿透。图3.17a-e显示了角焊点的变形(带有有限元网格)和未变形的形状,具有不同的裂纹长度:0.028、0.056、0.084、0.112和0.133 mm。裂纹尖端(裂纹长度= 0.112 mm)周围的典型von Mises应力轮廓如图3.18所示。可以看出,由于应力集中(图3.18),裂纹尖端的应力非常大。图3.19显示了角焊点的不同裂纹长度下,内部和外部裂纹尖端处的应力强度因子DKI(打开模式I)和DKII(剪切模式II)。可以看出,裂纹尖端的断裂特性主要由断裂的剪切模式决定(由于Si WLCSP和FR-4 PCB之间的热膨胀失配),尤其是在较大的裂纹长度处。3.9.2 Thermal Fatigue Life Prediction Model
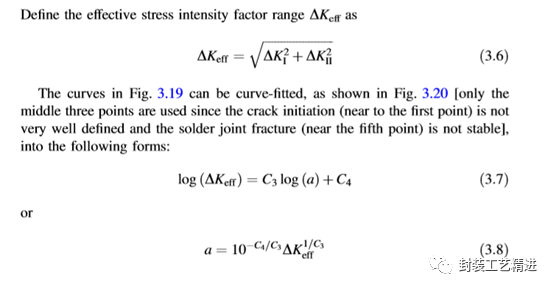
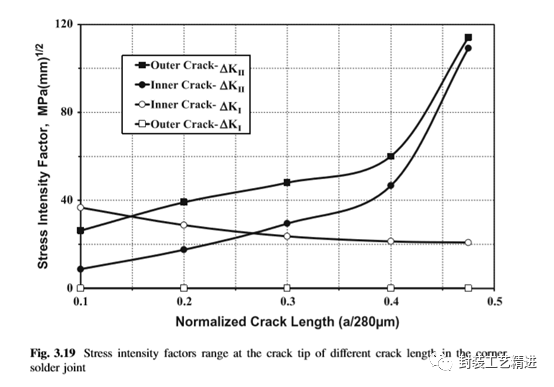
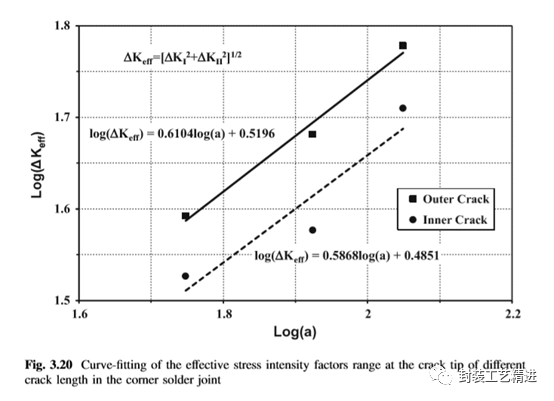
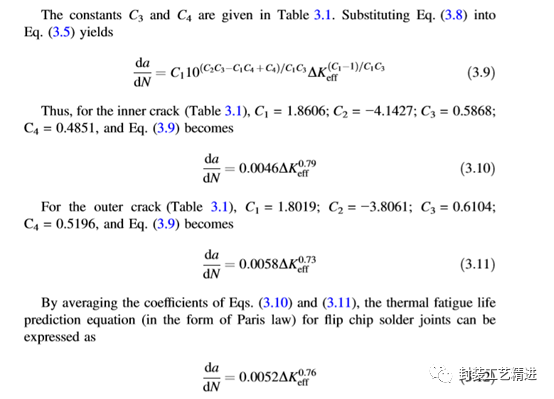
因此,对于给定的焊料凸点WLCSP组件,一旦通过计算模型确定了给定温度循环条件下的有效应力强度因子范围DKeff(针对裂纹长度(a)),就确定了失效循环数(N) 可以由等式估算 (3.12)。
3.9.3 Summary and Recommendations
用有限元方法通过断裂力学确定了角焊点不同裂纹长度的裂纹尖端处的应力强度因子。一些重要的结果总结如下:•在本研究中,角焊点裂纹在两个不同的位置发生,一个在芯片中心附近(内部裂纹),另一个在焊点的相对侧(外部裂纹)。这些裂纹恰好在PCB的铜焊盘上方。 •在较高的热循环下,角焊点的外部裂纹首先开始,并比内部裂纹稍大。 •在本研究中,角焊点的外部和内部裂纹在2000至2400个循环之间相遇。这表明PCB上的当前WLCSP即使没有填充胶,焊点也可在大多数工作条件下使用。 •对于所考虑的PCB上的WLCSP,已测量并确定了角焊点的裂纹长度与热循环次数的关系,如公式1所示。 (3.2)。同样,角焊点的热疲劳裂纹扩展速率由式(4)给出。 (3.4)就热循环次数或等式而言。 (3.5)就裂纹长度而言。 •对于所考虑的PCB上的WLCSP,已经确定了裂纹尖端处的有效应力强度因数范围,该范围是角焊点裂纹长度的函数,并由等式给出。 (3.8)。同样,就角焊点的有效应力强度因子范围而言,热疲劳裂纹的扩展速率由式(4)给出。 (3.9)。 •提出了一种新的用于倒装芯片焊点的热疲劳寿命预测模型,如方程式所示。 (3.12)。3.10 Fracture Characteristics of the CornerSolder Joint—Plastic Thermal Fatigue Life Prediction Model (DJ)
在这项研究中[19],假定焊料(63Sn–37Pb)是一种弹塑性材料,焊料的杨氏模量(图3.13)和应力-应变关系(图3.14)与温度有关。由于诸如焊料之类的可延展材料的大部分热疲劳寿命都用于传播裂纹(即,疲劳裂纹扩展),因此,焊点中不同裂纹长度的裂纹尖端周围的应力和应变(J积分)为 最大的兴趣。J积分以最简单的形式定义为与路径无关的线积分,用于测量裂纹尖端附近的奇异应力和应变的强度(图3.21)。以下等式以二维形式显示J的表达式。假定裂纹位于整体笛卡尔X–Y平面中,X平行于裂纹。在这项研究中,考虑了五个不同的裂纹长度。这些裂纹对称地位于PCB上的铜焊盘上方10 um处。在这项研究中使用了八节点的平面应变单元,单位是牛顿和毫米。在裂纹尖端,将中侧节点放置在四分之一点处,以捕获应力中的奇异性。3.10.1 Boundary Condition and Result
角焊点上施加的边界条件与本节中的完全相同。 3.9(图3.16)。图3.22a-e显示了角焊缝的变形(带有有限元网格)和未变形的形状,具有不同的裂纹长度:0.056、0.084、0.112、0.1225和0.133 mm。裂纹尖端(裂纹长度= 0.112 mm)周围的典型von Mises应力轮廓如图3.23所示。可以看出,由于应力集中,裂纹尖端处的应力非常大。图3.24显示了角焊点的不同裂纹长度的内部和外部裂纹尖端处的J积分。3.10.2 Thermal Fatigue Life PredictionModel
可以对图3.24中的曲线进行曲线拟合,如图3.25所示(由于焊点断裂(靠近第五点)不稳定,因此仅使用了四个点),其形式如下:因此,对于给定的焊料凸块WLCSP组件,一旦通过计算模型确定了给定温度循环条件下的裂纹长度(a)的J积分范围(DJ),则失效循环数(N )可以由等式估算。 (3.19)。3.10.3 Summary and Recommendations
•提出了一个简单的经验方程式,用于预测低成本PCB上焊有焊料的倒装芯片的热疲劳寿命。它是通过将测得的角焊点的热疲劳裂纹扩展速率与具有各种裂纹长度的角焊点的裂纹尖端处的模拟非线性断裂特性(J积分)相结合得出的。 •建议方程的使用非常简单。对于FR-4环氧PCB组件上任何给定的63Sn–37Pb凸点锡焊芯片,一旦通过计算模型确定了给定温度循环条件下的裂纹长度的J积分范围,就可以得出 焊点的失效可以通过所提出方程的积分来估计。 •为了验证所提出方程的准确性,需要进行更多的实验工作。这可以通过测试具有不同芯片尺寸和各种焊点几何形状的WLCSP来完成。3.11 Fracture Characteristics of the CornerSolder Joint—Creep Thermal Fatigue Life Prediction Model (DW)
3.11.1 Assumptions
在本研究中[18],假设焊料(63Sn–37Pb)是蠕变材料(图3.15)。同样,图3.16(角焊点)用于建模。由于Si,FR-4和焊料之间的整体/局部热膨胀失配,失配应力和应变(例如不同裂纹长度的裂纹尖端周围的蠕变应变能量密度)产生了导致焊点失效的驱动力。在这项研究中,考虑了三种不同的裂纹长度。这些裂纹对称地位于PCB上的铜焊盘上方10毫米处。在这项研究中使用八节点平面应变单元。如图3.27所示,在裂纹尖端处,三角形单元的中间节点位于四分之一点处,以捕获应力中的奇异性。接触元件用于模拟裂纹表面的闭合和滑动。3.11.2 Boundary Conditions
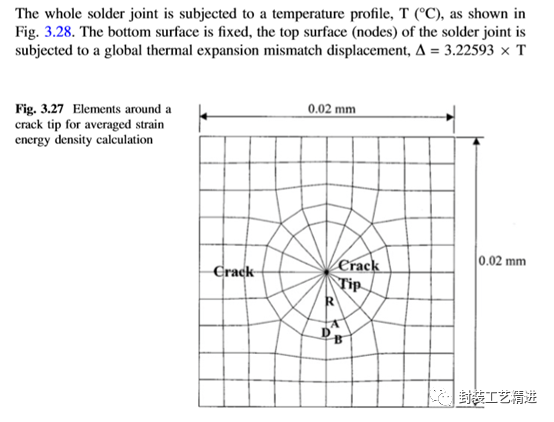
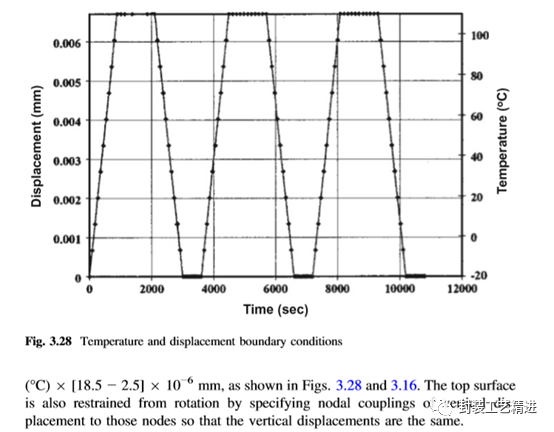
3.11.3 Deformed Shape, Stress, and Strain
图3.29a–c显示了角焊点的变形(带有有限元网格)和未变形的形状,具有不同的裂纹长度:0.056、0.084和0.112 mm。裂纹尖端(裂纹长度= 0.112 mm)周围的典型von Mises应力轮廓如图3.30所示。可以看出,由于应力集中,裂纹尖端处的应力非常大。图3.31、3.32和3.33显示了在三个完整的热循环过程中,角焊点的裂纹尖端(图3.29a,裂纹长度= 0.112 mm)之间的剪切蠕变应变历史,剪切应力历史以及剪切应力和剪切蠕变应变滞回曲线。可以看出,响应是收敛的。剪切蠕变应变范围为约0.33,剪切应力范围为约90MPa。图3.34、3.35和3.36显示了在三个完整角焊点的裂纹尖端(裂纹长度= 0.112 mm)附近的一点处的剪切蠕变应变历史,剪切应力历史以及剪切应力和剪切蠕变应变磁滞回线。热循环。同样,响应是收敛的。但是,正如预期的那样,剪切蠕变应变范围非常大(约0.72),剪切应力范围也非常大(约115 MPa)。3.11.4 Strain Energy Density Around theCrack Tip
从理论上讲,由于奇异性,裂纹尖端处的应变能密度是无穷大的。然而,实际上,裂纹尖端周围每个热循环的平均应变能密度用于确定焊点的热疲劳寿命。在这项研究中,裂纹尖端周围的应变能密度是通过在二维模型中将0.02 mm×0.02 mm的区域中的元素平均得到的,如图3.27所示。 (对于传统的焊锡凸焊芯片装配,铜焊盘的半径约为3-4密耳,共晶焊料的焊点高度约为1-2密耳,高温时的焊点高度约为3-4密耳 焊接,则平均应变能密度的面积应为0.008 mm×0.008 mm。)0.02 0.02 mm区域中大约有100个元素2。裂纹尖端用两行元素建模。第一行中的元素是三角形元素,中间节点倾斜到1/4点,如ANSYS建议的那样裂纹尖端奇异性的影响。第一行的半径为0.0037毫米,即正方形区域的一侧(0.02毫米)长度的大约20%,如图3.27所示(对于常规的倒装芯片装配,半径为 约0.0016毫米)。裂纹尖端周围有16个均匀的角度划分。第二排上的四边形元素的径向长度是第一排的一半。将为应变能密度计算中使用的剩余区域生成规则网格。在粘塑性过程中的任何时刻,该区域中元素的平均应变能密度均通过元素的体积进行归一化。其中Wt是时间点t的平均蠕变应变能量密度,Welement是每个元素的蠕变应变能量密度,在后处理中直接从ANSYS中提取,而Velement是每个元素的体积。但是,对于二维问题,ANSYS给出其中每个元素的体积通过假设单位厚度进行后处理。由时间t1至时间t2的完整热循环中的累积平均应变能密度由Wt2-Wt1计算。在这项研究中,开始和结束时t1 = 7200和t2 = 10,800 s分别使用第三周期的 图3.37显示了在第三次热循环中,围绕角焊点不同裂纹长度的内,外裂纹尖端周围的累积平均应变能密度范围。可以被看见裂纹长度越大,平均应变能密度范围越大。同样,对于给定的裂纹长度,外裂纹尖端周围的平均应变能密度范围大于内裂纹尖端周围的平均应变能密度范围。3.11.5 A New and Simple Thermal Fatigue Life Prediction Model
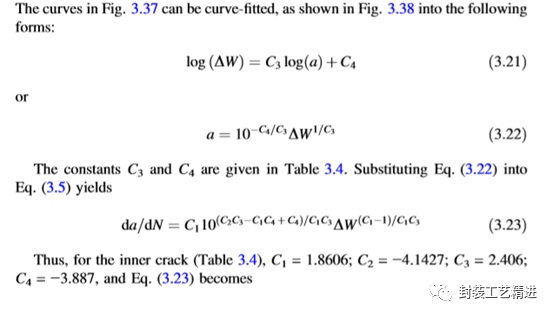
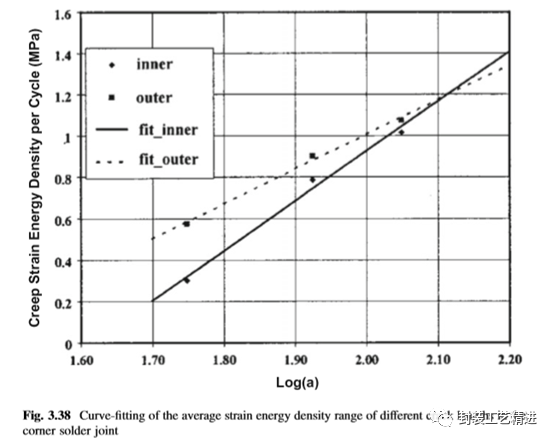
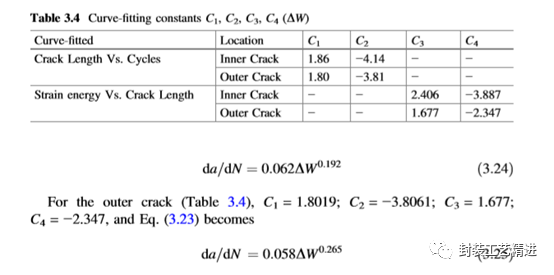
公式(3.24)和(3.25)如图3.39所示。通过平均等式的系数。 (3.24)和(3.25),WLCSP焊点的热疲劳寿命预测方程(图3.39)可以表示为因此,对于给定的焊料凸块倒装芯片组件,一旦通过计算模型确定了给定温度循环条件下根据裂纹长度(a)的平均应变能范围(DW),则失效循环数( N)可以由等式估算。 (3.26)。3.11.6 Summary and Recommendation
•提出了一个新的简单的经验方程式,用于预测低成本PCB上焊有焊料的倒装芯片的热疲劳寿命。它是通过将测得的角焊点的热疲劳裂纹扩展速率与模拟的非线性断裂特性*具有各种裂纹长度的角焊点的裂纹尖端周围的每个循环的平均应变能密度相结合得出的。 •建议方程的使用非常简单。对于任何给定的WLSCP PCB组件和PCB组件上的焊料凸焊倒装芯片,一旦通过计算模型确定了给定温度循环条件下每个热循环的平均应变能密度范围(以裂纹长度为单位),则角焊点失效的循环次数可以通过建议的方程* 8的积分来估算。 •对于WLCSP-PCB组件,建议使用元件尺寸和形状以及裂纹尖端周围的面积来计算平均应变能密度。对于PCB组件上的传统凸焊倒装芯片,还建议使用这些参数来确定平均应变能密度。3.12 Hitachi’s WLCSP
图3.40a显示了带有存储芯片的日立晶圆。如图3.40b所示,存储芯片上的原始焊盘间距很小,并沿芯片的中心线分布。
3.12.1 Hitachi’s WLCSP with Stress Relaxation Layer
金属RDL用于沿着晶片上芯片的中心线将细间距原始焊盘重新分布到芯片内部整个区域的更大间距区域排列的焊盘,如图3.40b所示。为了适用于较大的芯片(例如10 mm×10 mm)而没有下毛,Hitachi [54]在Si芯片和焊料凸块之间引入了应力松弛层,如图3.41所示。3.12.2 Key Process Steps for Hitachi’sWLCSP
图3.42显示了带有应力松弛层的日立WLCSP(表3.5)的关键工艺步骤。首先,在晶圆上旋涂光敏聚酰亚胺(P-PI),然后通过光刻技术打开芯片焊盘和切割道。然后,通过模版掩模在晶片上印刷液态树脂而在焊盘和切割道上没有开口,从而形成应力松弛层。树脂将流过开口边缘并形成光滑的斜面。为了在晶片上添加一层金属,Hitachi会在整个晶片上溅射种子金属(Cr和Cu),旋光化光致抗蚀剂层,并通过光刻技术打开互连的形状和新焊盘(以区域阵列格式) 。最后,通过电镀Cu和Ni形成互连和焊盘。通过蚀刻去除光致抗蚀剂和种子金属。现在,晶圆再次用P-PI旋涂,并且通过光刻技术打开了新的芯片焊盘和切割道。这次,P-PI就像阻焊层一样。助焊剂熔合后,将SnAgCu焊料凸点通过带有焊球安装器的模版掩模放置在晶片的新焊盘上。最后,将晶片倒入,清洗和切块。3.12.3 Reliability of Hitachi’s WLCSP
图3.43显示了日立WLCSP(10mm×10mm)WLCSP的温度循环测试(−55 $ 125°C)的寿命分布,没有填充),并在PCB上带有应力松弛层。可以看出,带有应力松弛层的WLCSP的表征寿命超过3000个循环。另一方面,在没有应力松弛层和填充层的情况下,相同芯片尺寸的表征寿命小于200个周期。
3.13 TSMC’s UFI WLCSP
为了节省一些工艺步骤,降低成本并降低封装轮廓,TSMC [55]在其WLCSP中取消了凸块下冶金(UBM),并将其称为UFI(无UBM集成)扇入式WLCSP。3.13.1 TSMC’s WLCSP with Protection Layer
图3.44a显示了常规的WLCSP,图3.44b显示了台积电的UFI WLCSP。可以看出,对于UFI WLCSP,聚合物2和UBM消失了。取而代之的是,引入聚合物复合保护层(PL)以固定焊料凸点。3.13.2 Key Process Steps for TSMC’s WLCS
在台积电的UFI WLCSP中,焊球直接安装在Cu RDL上,该RDL将电信号从芯片的原始焊盘传送到所需的区域阵列焊盘。然后,进行PL沉积以固定焊料凸点。3.13.3 Reliability of TSMC’s WLCSP
图3.45显示了TSMC UFIWLCSP在PCB上的热循环结果的寿命分布。台积电[55]发现是因为:(1)力学支持PL,(2)控制最大应变位置,以及(3)在材料优化方面,UFI WLCSP焊点可靠(特征寿命超过800次循环,并且热循环发生在温度范围内) -40和+125°C,每小时一个循环)即使最大芯片尺寸为10.3毫米至10.3毫米而没有填充。3.14 Summary and Recommendations
WLCSP面临来自FOWLP的激烈竞争。由于(1)缩小芯片尺寸以降低器件晶片成本,以及(2)更多的功能要内置到芯片中(从而增加引脚输出)以提高效率,所以没有足够的空间扇入芯片所有的垫子。 这与希望采用系统级封装(SiP)来提高性能和降低成本的愿望/要求更加复杂,一些市场份额已经并且将被FOWLP夺走。 图3.47显示了来自智能手机HTC Desire 606 W(SPREADTRUM SC8502)的SiP,它是由FOWLP技术制成的。 SiP尺寸为7.4毫米7.4毫米0.71毫米,由2.8毫米2.8毫米调制解调器和3毫米3毫米应用处理器组成。有2个RDL。
- The End -
声明:欢迎转发本号原创内容,转载和摘编需经本号授权并标注原作者和信息来源为云脑智库。本公众号目前所载内容为本公众号原创、网络转载或根据非密公开性信息资料编辑整理,相关内容仅供参考及学习交流使用。由于部分文字、图片等来源于互联网,无法核实真实出处,如涉及相关争议,请跟我们联系。我们致力于保护作者知识产权或作品版权,本公众号所载内容的知识产权或作品版权归原作者所有。本公众号拥有对此声明的最终解释权。
投稿/招聘/推广/合作/入群/赞助 请加微信:15881101905,备注关键词
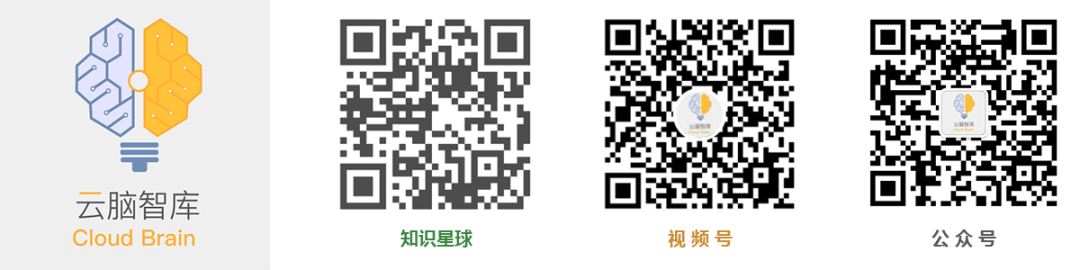
微群关键词:天线、射频微波、雷达通信电子战、芯片半导体、信号处理、软件无线电、测试制造、相控阵、EDA仿真、通导遥、学术前沿、知识服务、合作投资.
“阅读是一种习惯,分享是一种美德,我们是一群专业、有态度的知识传播者.”
↓↓↓ 戳“阅读原文”,加入“知识星球”,发现更多精彩内容.
/// 先别走,安排点个“赞”和“在看” 吧!↓↓↓