点击上面↑“电动知家”可以订阅哦!
一、锂离子电池生产流程详解
锂离子电池的生产制造,是由一个个工艺步骤严密联络起来的过程。
锂电池的生产工艺比较复杂,主要生产工艺流程主要涵盖电极制作的搅拌涂布阶段(前段)、电芯合成的卷绕注液阶段(中段),以及化成封装的包装检测阶段(后段),价值量(采购金额)占比约为(35~40%):(30~35)%:(30~35)%。
差异主要来自于设备供应商不同、进口/国产比例差异等,工艺流程基本一致,价值量占比有偏差但总体符合该比例。
锂电生产前段工序对应的锂电设备主要包括真空搅拌机、涂布机、辊压机等;中段工序主要包括模切机、卷绕机、叠片机、注液机等;后段工序则包括化成机、分容检测设备、过程仓储物流自动化等。除此之外,电池组的生产还需要Pack自动化设备。
锂电池前端工艺的结果是将锂电池正负极片制备完成,其第一道工序是搅拌,即将正、负极固态电池材料混合均匀后加入溶剂,通过真空搅拌机搅拌成浆状。
配料的搅拌是锂电后续工艺的基础,高质量搅拌是后续涂布、辊压工艺高质量完成的基础。
涂布和辊压工艺之后是分切,即对涂布进行分切工艺处理。
如若分切过程中产生毛刺则后续装配、注电解液等程序、甚至是电池使用过程中出现安全隐患。
因此锂电生产过程中的前端设备,如搅拌机、涂布机、辊压机、分条机等是电池制造的核心机器,关乎整条生产线的质量,因此前端设备的价值量(金额)占整条锂电自动化生产线的比例最高,约35%。
锂电池制造过程中,中段工艺主要是完成电池的成型,主要工艺流程包括制片、极片卷绕、模切、电芯卷绕成型和叠片成型等,是当前国内设备厂商竞争比较激烈的一个领域,占锂电池生产线价值量约30%。
目前
动力锂电池
的电芯制造工艺主要有卷绕和叠片两种,对应的电池结构形式主要为圆柱与方形、软包三种,圆柱和方形电池主要采用卷绕工艺生产,软包电池则主要采用叠片工艺。圆柱主要以18650和26650为代表(Tesla单独开发了21700电池、正在全行业推广),方形与软包的区别在于外壳分别采用硬铝壳和铝塑膜两种,其中软包主要以叠片工艺为主,铝壳则以卷绕工艺为主。
软包结构形式主要面向中高端数码市场,单位产品的利润率较高,在同等产能条件下,相对利润高于铝壳电池。由于铝壳电池易形成规模效应,产品合格率及成本易于控制,目前二者在各自市场领域均有可观的利润,在可以预见的未来,二者都很难被彻底取代。
由于卷绕工艺可以通过转速实现电芯的高速生产,而叠片技术所能提高的速度有限,因此目前国内动力锂电池主要采用卷绕工艺为主,因此卷绕机的出货量目前大于叠片机。
卷绕和叠片生产对应的前道工序为极片的制片和模切。
制片包括对分切后的极片/极耳焊接、极片除尘、贴保护胶纸、极耳包胶和收卷或定长裁断,其中收卷极片用于后续的全自动卷绕,定长裁断极片用于后续的半自动卷绕;
冲切极片是将分切后的极片卷绕冲切成型,用于后续的叠片工艺。
在锂电封装焊接方面,联赢、大族、光大的主流激光技术集成应用厂家均有所涉及,能够满足需求、无需进口。
锂电后段生产工艺主要为分容、化成、检测和包装入库四道工序,占生产线价值量约35%。化成和分容作为后段工艺中最主要环节,对成型的电池进行激活检测,由于电池的充放电测试周期长,因此设备的价值量最高。化成工艺的主要作用在于将注液封装后的电芯充电进行活化,分容工艺则是在电池活化后测试电池容量及其他电性能参数并进行分级。化成和分容分别由化成机和分容机通常由自动化分容化成系统完成。
动力电池组系统是将众多单个的电芯通过串、并联的方式连接起来的电池组,综合了动力和热管理等电池硬件系统。Pack是动力电池系统生产、设计应用的关键,是连接上游电芯生产和下游整车的应用核心环节,通常设计需求由电芯厂或汽车厂提出,通常由电池厂、汽车厂或者第三方Pack厂完成。
锂电池Pack产线相对简单,核心工序包括上料、支架粘贴、电焊、检测等工艺,核心设备为激光焊接机以及各类粘贴检测设备。目前,各大锂电设备厂商在此领域的自动化集成布局较少,而大族激光、联赢激光等激光设备厂商由于在激光领域的绝对优势,在Pack设备领域占有率较高。
目前Pack生产的自动化比例相对较低,是因为目前的新能源车单款车销量都不够大,上自动化生产线的成本较高。
磷酸铁锂和三元:能量密度绕不开的话题,不同材料需要全套设备投资
目前国内主流动力锂电池的正极材料分为磷酸铁锂和三元两大种类。其中磷酸铁锂是目前最安全的
锂离子电池
正极材料,其循环寿命通常在2000次以上,再加上由于产业成熟而带来的价格和技术门槛的下降,使得很多厂商出于各种因素考虑都会采用
磷酸铁锂电池
。然而磷酸铁锂电池在能量密度方面则存在明显的缺陷,目前磷酸铁锂电池龙头比亚迪磷酸铁锂单体电芯能量密度为150Wh,2017年底比亚迪预计将能量密度提升到160Wh,理论上磷酸铁锂能量密度很难超过200Gwh。
三元聚合物锂电池
是指正极材料使用镍钴锰酸锂的锂电池,镍钴锰的实际比例可以根据具体需要进行调整。由于三元锂电池具备更高的能量密度(目前宁德时代等动力电池一流大厂三元锂电池能量密度普遍能达到200Wh/kg-220Wh/kg,业内预计到2020年三元电池单体电芯能量密度将达到300Wh/kg的水平),乘用车市场开始转向三元锂电池,而在安全性要求更高的客车上,磷酸铁锂则更受青睐。随着全电动乘用车的发展,三元锂电池正在占据越来越重要的位置。
两种材料的能量密度和成本有差异,不同的汽车、不同的车企有不同的选择。二者在生产工艺流程上大致相同,区别主要体现在材料的使用和配比上不同、具体工艺参数差异较大,设备无法共线生产,且单纯改造切换产能的成本较高(三元材料对真空除湿等要求严格,之前的磷酸铁锂生产线基本没有除湿要求),因此多家电芯厂在产能规划中会同时布局、分别采购设备。
锂电池浆料性质及关键影响因素分析
锂离子电池电极浆料是流体的一种,通常流体可以分为牛顿流体和非牛顿流体。其中,非牛顿流体又可分为胀塑性流体、依时性非牛顿流体、假塑性流体和宾汉塑性流体等几种。
牛顿流体是指在受力后极易变形,且切应力与变形速率成正比的低粘性流体。任一点上的剪应力都同剪切变形速率呈线性函数关系的流体。自然界中许多流体是牛顿流体。如:水、酒精等大多数纯液体、轻质油、低分子化合物溶液以及低速流动的气体等均为牛顿流体。
非牛顿流体,是指不满足牛顿黏性实验定律的流体,即其剪应力与剪切应变率之间不是线性关系的流体。非牛顿流体广泛存在于生活、生产和大自然之中。高分子聚合物的浓溶液和悬浮液等一般为非牛顿流体。绝大多数生物流体都属于现在所定义的非牛顿流体。人身上血液、淋巴液、囊液等多种体液,以及像细胞质那样的“
半流体”
都属于非牛顿流体。
电极浆料是一种是由多种不同比重、不同粒度的原料组成,又是固-
液相混合分散,形成的浆料属于非牛顿流体。锂电池浆料又可分为正极浆料和负极浆料两种,由于浆料体系(油性、水性)不同,其性质必千差万别。但是,判断浆料的性质无非以下几个参数:
1.浆料的粘度
粘度是流体粘滞性的一种量度,是流体流动力对其内部摩擦现象的一种表示。
液体在流动时,在其分子间产生内摩擦的性质,称为液体的黏性,粘性的大小用黏度表示,是用来表征液体性质相关的阻力因子。粘度又分为动力黏度和条件粘度。
粘度的定义为一对平行板,面积为A,相距dr,板间充以某液体。今对上板施加一推力F,使其产生一速度变化du。由于液体的粘性将此力层层传递,各层液体也相应运动,形成一速度梯度du/dr,称剪切速率,以r′表示。F/A称为剪切应力,以τ表示。剪切速率与剪切应力间具有如下关系:
(F/A)=η(du/dr)
牛顿流体符合牛顿公式,粘度只与温度有关,与切变速率无关,τ与D为正比关系。
非牛顿流体不符合牛顿公式τ/D=f(D),以ηa表示一定(τ/D)下的粘度,称表观粘度。非牛顿液体的粘度除了与温度有关外,还与剪切速率、时间有关,并有剪切变稀或剪切变稠的变化。
2.浆料性质
浆料是一种非牛顿流体,是固液混合流体,为了满足后续涂布工艺的要求,浆料需要具有以下三个特性:
①好的流动性。流动性可以通过搅动浆料,让其自然流下,观察其连续性。连续性好,不断断续续则说明流动性好。流动性与浆料的固含量和粘度有关,
②流平性。浆料的流平性影响的是涂布的平整度和均匀度。
③流变性。流变性是指浆料在流动中的形变特征,其性质好坏影响着极片质量的优劣。
3.浆料分散基础
锂离子电池的电极制造,正极浆料由粘合剂、导电剂、正极材料等组成;负极浆料则由粘合剂、石墨碳粉等组成。正、负极浆料的制备都包括了液体与液体、液体与固体物料之间的相互混合、溶解、分散等一系列工艺过程,而且在这个过程中都伴随着温度、粘度、环境等变化。锂离子电池浆料的混合分散过程可以分为宏观混合过程和微观分散过程,这两个过程始终都会伴随着锂离子电池浆料制备的整个过程。浆料的制备一般会经过以下几个阶段:
①
干粉混合
。颗粒之间以点点、点面、点线形式接触,
②半干泥状
捏合阶段
。此阶段在干粉混合均匀之后,加入粘结剂液体或溶剂,原材料被润湿、呈泥状。经过搅拌机的强力搅拌,物料受到机械力的剪切和摩擦,同时颗粒之间也会有内摩擦,在各个作用力下,原料颗粒之间趋于高度分散。此阶段对于成品浆料的粒度和粘度有至关重要的影响。
③
稀释分散阶段
。捏合完成之后,缓慢加入溶剂调节浆料粘度和固含量。此阶段分散与团聚共存,并最后达到稳定。在这个阶段物料的分散主要受机械力、粉液间摩擦阻力、高速分散剪切力、浆料与容器壁撞击相互作用力的影响。
二、影响浆料性质的参数分析
合浆后的浆料需要具有较好的稳定性,这是电池生产过程中保证电池一致性的一个重要指标。随着合浆结束,搅拌停止,浆料会出现沉降、絮凝聚并等现象,产生大颗粒,这会对后续的涂布等工序造成较大的影响。表征浆料稳定性的主要参数有流动性、粘度、固含量、密度等。
1. 浆料的粘度
电极浆料需要具有稳定且恰当的粘度,其对极片涂布工序具有至关重要的影响。粘度过高或过低都是不利于极片涂布的,粘度高的浆料不容易沉淀且分散性会好一点,但是过高的粘度不利于流平效果,不利于涂布;粘度过低也是不好的,粘度低时虽然浆料流动性好,但干燥困难,降低了涂布的干燥效率,还会发生涂层龟裂、浆料颗粒团聚、面密度一致性不好等问题。
在我们生产过程中经常出现的问题是粘度出现变化,而这里的“
变化”
又可分为:瞬时变化和静止变化。瞬时变化是指在粘度测试过程中间就出现了剧烈的变化,静止变化是指浆料静止放置一段时间后粘度出现变化。粘度的变化或高或低,或时高时低。通常来说,影响浆料粘度的因素主要有搅拌浆料的转速、时间控制、配料顺序、环境温湿度等。因素很多,当我们遇见粘度变化时应该怎样分析解决呢?浆料的粘度本质上,是由粘结剂决定性影响的。假想,没有粘结剂PVDF/CMC/SBR
(如图2、3)
,或者粘结剂没有很好的将活物质组合起来,固体活物质会与导电剂构成具有均匀涂覆的非牛顿流体吗?不会!所以,分析解决浆料粘度变化的原因,要从粘结剂的本质及浆料分散程度上着手。
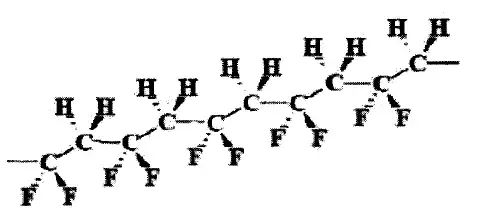
图2.PVDF分子排列结构
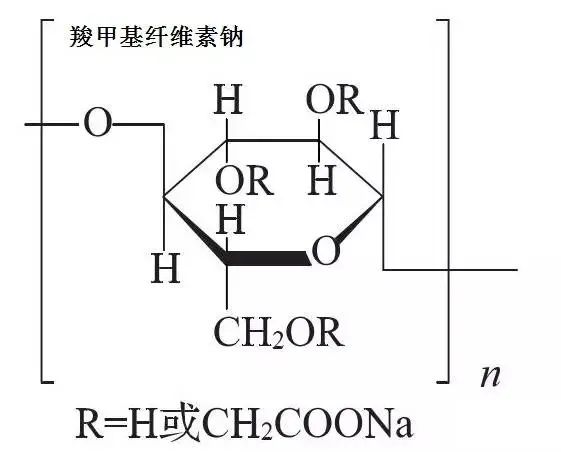
图3.CMC分子结构式
(1)粘度升高
不同的浆料体系具有不同的粘度变化规律,目前主流的浆料体系是正极浆料PVDF/NMP油性体系,负极浆料是石墨/CMC/SBR水性体系。
①正极浆料在放置一段时间后粘度升高。其原因一(短时间放置)是浆料搅拌速度过快,粘结剂未充分溶解,放置一段时间后PVDF粉末充分溶解,粘度升高。通常来说,PVDF需要至少3个小时才能充分溶解,无论多快的搅拌速度都无法改变这一影响因素,所谓“欲速则不达”。原因之二(长时间放置)是浆料静置过程中,胶体由溶胶状态变为凝胶状态,此时如果对其进行慢速匀浆,其粘度可以恢复。原因之三是胶体与活物质、导电剂颗粒之间形成了一种特殊的结构,此状态是不可逆的,浆料粘度升高后无法恢复。
②负极浆料粘度升高。负极浆料粘度升高主要是由粘结剂分子结构被破坏引起的,分子链断裂后被氧化后浆料粘度升高。如果物料被过度分散,颗粒粒径产生较大的降低,也会增加浆料的粘度。
(2)粘度降低
①正极浆料粘度降低。原因之一,粘结剂胶体发生了性状的变化。变化的原因多种多样,如浆料传输过程中受到强剪切力、粘结剂吸收水分发生质变、搅拌过程中导致结构发生变化、自身发生降解等。原因之二,搅拌分散不均匀导致浆料中固体物质大面积沉降。原因之三,搅拌过程中粘结剂受到设备和活物质的强剪切力和摩擦力,在高温情况下发生性状变化,造成粘度下降。
②负极浆料粘度降低。原因之一
CMC
中混有杂质,
CMC
中的杂质大多是难溶性高分子树脂,当
CMC
与钙、镁等混溶时,会降低其粘度。原因之二
CMC
是羟甲基纤维素钠,其主要是
C/O
的结合,键强很弱极易被剪切力破坏,当搅拌速度过快或时间太长时有可能
破坏CMC的结构
。
CMC
在负极浆料中起到增稠和稳定的作用,同时对原材料的分散起重要的作用,其结构一旦发生破坏,必然引起浆料沉降,粘度降低。原因之三是
SBR
粘结剂的破坏。在实际生产中通常选择
CMC
和
SBR
协同工作,此二者的作用各不相同。
SBR
主要起到粘结剂的作用,但是其在长时间搅拌下极易发生破乳,导致粘结性失效,浆料粘度降低。
(3)特殊情况(果冻状及时高时低)
在正极浆料制备过程中有时候会出现浆料变成“果冻”的情况。这种情况的原因主要有二:其一,水分。考虑活物质吸潮、搅拌过程水分控制不好,原材料吸收水分后或者搅拌环境湿度较高,导致PVDF
吸收水分变成果冻状。其二,
浆料或材料的pH值
。pH
值越高,对水分的控制就要求更严格,尤其是NCA
、 NCM811
等高镍材料的搅拌。
浆料粘度忽高忽低,原因之一可能是浆料测试过程中未完全稳定下来,浆料粘度受温度的影响很大。尤其是被高速分散之后,浆料内部温度存在一定的温度梯度,取样不同粘度也不尽相同。原因之二是浆料的分散性差,活物质、粘结剂、导电剂没有良好的分散开,浆料就没有好的流动性,自然浆料粘度忽高忽低。
2. 浆料的粒度
在合浆之后,需要对其粒度进行测量,粒度测量的方法通常采用刮板法。粒度是表征浆料质量的一个重要参数,粒度大小对于涂布工序、辊压工序以及电池性能有重要影响,理论上来说浆料粒度越小越好。当颗粒粒径过大时,浆料的稳定性会受到影响,出现沉降、浆料一致性不良等。在挤压式涂布过程中会出现堵料、极片干燥后麻点等情况,造成极片质量问题。在后续的辊压工序中,涂布不良处由于受力不均,
极易造成极片断裂、局部微裂纹
,这对电池的循环性能、倍率性能和安全性能造成了极大的危害。
正负极活物质、粘接剂、导电剂等主材料粒径大小不一,密度不同,在搅拌过程中会出现混合、挤压、摩擦、团聚等多种不同的接触方式
。在原材料被逐渐混匀、被溶剂润湿、大块物料破裂和逐渐趋于稳定这几个阶段中,会出现物料混合不匀、粘接剂溶解不良、细颗粒严重团聚、粘接剂性状发生变化等情况,就会导致大颗粒的产生。
当我们弄明白颗粒出现的原因时就要对症下药,解决这些问题。关于物料干粉混合,个人觉得搅拌机速度对干粉混合程度影响不大,但是两者需要足够的时间来保证干粉的混匀。现在有的厂家选择粉状粘接剂有的选择液体溶解好的粘接剂,两种不同的粘接剂决定了工艺的不同,采用粉状粘结剂需要更长的时间来进行溶解,否则在后期会出现溶胀、回弹、粘度变化等。细颗粒之间的团聚不可避免,但是我们要保证物料之间有足够大的摩擦力,能够促使团聚颗粒出现挤压、破碎,利于混合。这就需要我们控制好浆料不同阶段的固含量,太低的固含量会影响颗粒之间的摩擦分散。
3. 浆料的固含量
浆料的固含量和浆料稳定性息息相关,同种工艺与配方,浆料固含量越高,粘度越大,反之亦然。在一定范围内,粘度越高,浆料稳定性越高。我们设计电池时,一般从电池容量反推卷芯厚度再到极片的设计,那么极片设计仅仅与面密度、活物质密度、厚度等参数有关。极片的参数是通过涂布机和辊压机对其进行调整的结果,浆料的固含量对其并无直接影响。那么,浆料固含量的高低是不是就无关紧要呢?
(1
)固含量对于提高搅拌效率和涂布效率具有一定影响。固含量越高,浆料搅拌时间越短,所耗溶剂越少,涂布干燥效率越高,节省时间。
(2
)固含量对设备有一定的要求。高固含量浆料对设备的损耗较高,因为固含量越高,设备磨损越严重。
(3
)高固含量的浆料稳定性更高,部分浆料稳定性测试结果表明(如下图),常规搅拌的TSI(
不稳定性指数)1.05
要高于高粘度搅拌工艺TSI
值0.75
,所以高粘度搅拌工艺所获得的浆料稳定性要优于常规搅拌工艺。但是高固含量的浆料也会影响其流动性,非常挑战涂布工序的设备和技术人员。

(4)高固含量的浆料可以减少涂层间厚度,降低电池内阻。
4. 浆料密度
浆料的密度是反应浆料一致性的重要参数,通过测试不同位置的浆料密度可以验证
浆料的分散效果。在这就不多赘述,通过以上的总结,相信大家制备出良好的电极浆料。
三、导电剂的介绍
1. 原理:增加电极颗粒之间的接触,从而提高了电极的导电率。
①在极片制作时通常加入一定量的导电剂,在活性物质之间、活性物质与集流体之间起到收集微电流的作用,以减小电极的接触电阻,加速电子的移动速率;
②导电剂也可以提高极片加工性,促进电解液对极片的浸润;
③同时也能有效地提高锂离子在电极材料中的迁移速率,降低极化,从而提高电极的充放电效率和锂电池的使用寿命。
①优点:炭黑在扫描电镜下呈链状或葡萄状,单个炭黑颗粒具有非常大的比表面积,堆积紧密有利于颗粒之间紧密接触在一起,组成了电极中的导电网络,有利于电解质的吸附而提高离子电导率。
②缺点:比表面较大带来的工艺问题是分散困难、具有较强的吸油性,这就需要通过改善活物质、导电剂的混料工艺来提高其分散性,并将炭黑量控制在一定范围内(通常是1.5%以下)。
4. 导电石墨:KS-6、KS-15、SFG-6、SFG-15等。
①石墨导电剂基本为人造石墨,与负极材料人造石墨相比,作为导电剂的人造石墨具有更小的颗粒度,一般为3~6μm,且孔隙和比表面更发达,也具有较好的导电性,其本身颗粒较接近活物质颗粒粒径,颗粒与颗粒之间呈点接触的形式,可以构成一定规模的导电网络结构,有利于改善极片颗粒的压实(个人认为,可能是因为其分子间作用力,此外,还可以通过减少导电剂用量,达到增大极片压实的目的)以及提高离子和电子电导率,同时用于负极时更可提高负极容量。
②导电石墨具有更好的压缩性和分散性,可提高电池的体积能量密度和改善极片的工艺特性, 一般配合炭黑使用。
①导电碳纤维具有线性结构,在电极中容易形成良好的导电网络,表现出较好的导电性,因而减轻电极极化,降低电池内阻及改善电池性能。在碳纤维作为导电剂的电池内部,活物质与导电剂接触形式为点线接触,相比于导电炭黑与导电石墨的点点接触形式,不仅有利于提高电极导电性,更能降低导电剂用量,提高电池容量。
②VGCF杂质极少,在正极添加剂方面也能够放心使用。如将VGCF添加在电极(正极、负极)上,VGCF有很大的长径比,即使正、负极活性材料膨胀收缩后,其活性材料颗粒之间的间隙,可以有VGCF架桥连接,电子与离子传输不会间断,可大幅度提高电极的导电性。
③由于纳米碳纤维VGCF 微结构是中空,可以让正负电极吸纳更多的电解液,使得锂离子可以顺利快速嵌入,有利于高倍率充放电。
④VGCF是高强度纤维状长径比大的材料,可以增加电极板的可绕性,正负极活性材料颗粒之间粘结力更强,不会因为绕曲而龟裂掉粉,可提高电极的强度。
⑤高导电导热特性,正极活性材料其导电性不好,添加纳米碳纤维以提高正极活性导电性,也提高正负极导热系数,利于散热。
①碳纳米管具有良好的电子导电性,纤维状结构能够在电极活性材料中形成连续的导电网络,其与活性物质也是呈点线接触形式,可以在锂电池电极活性物质颗粒之间形成大量的导电接触位点,减小电极材料颗粒间的接触阻抗,具有在导电网络中充当“导线”的作用,而且它具有双电层效应,能够发挥超级电容器的高倍率特性。
②添加碳纳米管后极片有较高的韧性, 能改善充放电过程中材料体积变化而引起的剥落, 提高循环寿命.碳纳米管可大幅度提高电解液在电极材料中的渗透能力。
③其良好的导热性能还有助于电池充放电时散热,降低电池极化,改善电池高低温性能,提升电池循环性能。
④缺点:由于其直径小、长径比大, 在范德华力的作用下,极易发生团聚,影响其导电效果,故需要解决的主要问题是CNT的分散性,要求其在浆料中要分散良好。目前可以通过高速剪切、添加分散剂、做成分散浆料、超细磨珠静电分散等工艺解决。
①石墨烯单独作为负极材料时,虽然其初始容量较高,但是随着充放电,电池的容量快速衰减,这可能是较大的比表面积,以及较多结构缺陷,使得石墨烯与电解液之间的副反应较多,从而导致不可逆容量较高。(因此目前锂离子电池中石墨烯的应用主要集中在石墨烯作为导电剂添加,以提高导电性,以及制备石墨烯复合材料。例如石墨烯与Si材料结合,制备具有多孔结构的Si-G复合材料。)
②石墨烯作为新型导电剂,由于其独特的片状结构(二维结构),与活性物质的接触为点面接触而不是常规的点点接触形式,这样可以最大化的发挥导电剂的作用,减少导电剂的用量,从而可以多使用活性物质,提升锂电池容量。
③作为导电剂的效果与其加入量密切相关. 在加入量较小的情况下, 石墨烯由于能够更好地形成导电网络, 效果远好于导电炭黑。但是片层较厚的石墨烯会阻碍锂离子的扩散而降低极片的离子电导率(一般认为6-9层最为适宜,单层石墨烯只有一个碳原子的厚度,即0.335纳米,相当于一根头发的20万分之一的厚度,1毫米厚的石墨中将将近有150万层左右的石墨烯)。
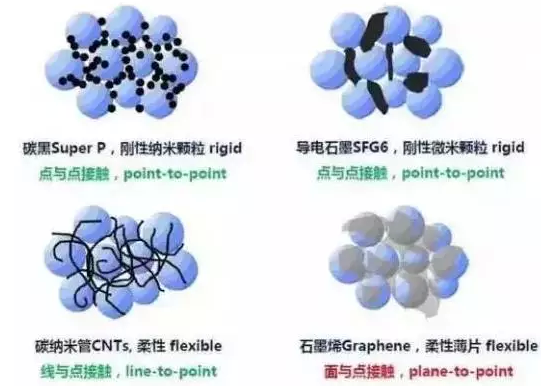
导电剂在电极中的作用是提供电子移动的通道,导电剂含量适当能获得较高的放电容量和较好的循环性能,含量太低则电子导电通道少,不利于大电流充放电;太高则降低了活性物质的相对含量,使电池容量降低。
导电剂的存在可以影响电解液在电池体系内的分布,由于受锂离子电池的空间限制,注入的电解液量是有限的,一般是处于贫液状态,而电解液作为电池体系内部连接正负极的离子体,其分布对锂离子在液相中的迁移扩散有着至关重要的影响。当一端电极中导电剂含量过高时,电解液富集在这一端而使另一端的锂离子传输过程缓慢,极化度较高,在反复循环后易于失效,从而影响电池的整体性能。
四、锂枝晶的形成机理与防治
枝晶锂简单来说,就是石墨中所嵌入的锂的含量超过了它所承受的范围,多余的锂离子就会和负极中穿梭而来的电子结合,在负极表面上开始沉积。在给电池充电的过程中,外界给予电池一个电压,使得正极材料内部的锂离子得以脱出进入电解液介质中,同样电解液中的锂离子会在外界电压差的条件下向碳层移动,由于石墨是具有层状通道的,锂便会进入通道与碳形成碳锂化合物,形成LiCx(x=1~6)这类石墨层间化合物。锂电池负极上的电化学反应可以用下式表示:
在这个公式中,有一个参数即x+§,如果两者之和x+§≥1,就会产生枝晶锂。在这里有一个大家都熟悉的概念,石墨层间化合物。石墨层间化合物(简称GICs)是一种利用物理或化学(这里是外界给予的一个电压)的方法使非炭质反应物插入石墨层间,与炭素的六角网络平面结合的同时又保持了石墨层状结构的晶体化合物。
枝晶锂一般沉积于隔膜和负极的接触位置上,有过拆解电池经验的同学应该常常发现隔膜上有一层灰色的物质,没错那就是析锂了。枝晶锂是锂离子接收电子后形成的锂金属,锂金属无法再形成锂离子参与电池的充放电反应,造成电池容量降低。枝晶锂是从负极表面向着隔膜的方向生长的,如果锂金属不断地沉积,最终会刺穿隔膜造成电池短路,引发电池安全问题。
影响枝晶锂的形成因素主要有:负极表面的粗糙程度、锂离子浓度梯度、电流密度等,此外,SEI膜、电解液的种类、溶质浓度、正负极之间有效距离等都对枝晶锂的形成有一定影响。
负极表面的粗糙程度影响枝晶锂的形成,表面越粗糙越有利于形成枝晶锂。负极表面出现晶核后,晶核石墨表面的接触角θ越小,体相吉布斯自由能越大,所需的临界过电势就越小,更有利于枝晶锂的形成;
锂离子从正极材料中脱出后,穿过电解液和隔膜,在负极接受电子。在充电过程中,正极的锂离子浓度逐渐增加,负极的锂离子浓度则因为不断接受电子而减少,在电流密度大的稀溶液中,离子浓度会变为0,在此基础上Fleury et al.和Chazalviel建立模型表明当离子浓度降低到0时,负极将形成局部空间电荷(个人认为是因为形成电位差,导致负极中电子逸出),并形成枝晶结构,枝晶结构生长速度和电解液中离子偏移速率相同。
③电流密度:有些文章认为,枝晶锂的针尖生长速度与电流密度密切相关。如果降低电流密度,可以在一定程度上延缓枝晶锂的生长。
④限制电镀电位低于临界值,另外对于传统的充放电机制可以进行改善,比如可以考虑使用脉冲方式。
国务院正式发布:《新能源汽车产业发展规划(2021—2035年)》(附解读)
大玩家来了!苹果汽车跑步入场,百年汽车正在被颠覆!
行贿广汽集团高层,性侵员工,侮辱中国籍员工,CEO被实名举报
涉权色交易,回扣等,北汽某副职领导被公开举报,细节曝光!
缓发工资、绩效考核!这家新势力搞“高管带货”“全员卖车”
特斯拉“电池日”全解读:续航提升54%,成本下降56%,投资下降69%.....
电动
知
家,一个有价值的微信公众号!
更多
新能源电动汽车、无人驾驶
最新行
业资讯和专业知识,请关注“电动知家”微信公众号(微信号ev_home)。
给大家推荐一款比较好用的语音转文字工具,今天正好在整理素材的时候,发现了一个音频素材,自己边听边写效率好低,所以就从小程序里找了一个语音转文字的工具,导入后很快就转写出来了,非常方便实用,而且是免费的,同时还支持实时录音转文字,一边说话,同时说话内容就出来了,比较适合开会时录音,非常方便实用,推荐给有需要的人。
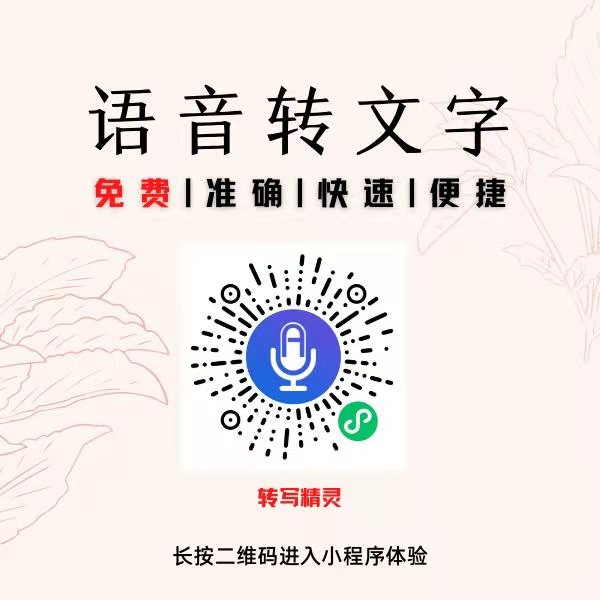