
群:如需申请内外饰、车身、座椅、智能制造等专业群请添加微信GSAuto0001验证信息后要求进群。
征稿:关于汽车新材料、新工艺、新技术的文稿,请发送至gearshare@163.com
社群推荐:GSAuto联盟|座椅技术专家委员会招新了
热门推荐:
【汽车工艺】汽车制造中多种焊接方法大总结,就一个字,全!【汽车设计】主流汽车零部件产品开发项目管理方法对比【汽车工艺】16家车企揭示的中国汽车制造工业4.0现状(内附评估模型)【汽车工艺】各种焊接技术知识汇总,20分钟全搞定!【汽车工艺】汽车轻量化高端汽车铝合金冲压板材的应用【汽车设计】车载动力电池包的有限元分析及轻量化设计【汽车工艺】焊接工艺问题及解决措施
【汽车工艺】焊接质量控制,这些内容SQE要掌握
【汽车设计】纯电动乘用车动力电池包整车布置集成研究【汽车工艺】从1—10的一体化压铸:投产元年
【汽车工艺】特斯拉压铸工艺解析
【汽车工艺】特斯拉车身材料及工艺解析
【汽车工艺】模具行业专题研究:大型一体压铸的技术核心
【汽车工艺】汽车铝合金车身连接工艺方法大全
【汽车工艺】全铝车身结构与材料应用及连接工艺剖析(奥迪、蔚来汽车、奇瑞捷豹路虎、通用凯迪拉克)
【汽车工艺】汽车总装工艺的总体布局
【汽车工艺】焊装车间——车身工艺流程介绍
【汽车工艺】不同铸造工艺对产品结构的影响
【汽车工艺】纯电动汽车与传统汽车总装工艺对比分析
【汽车工艺】低成本汽车车身试制夹具的敏捷开发
【汽车工艺】汽车总装工艺流程的设计
【汽车工艺】一种3mm厚汽车热成形产品
【汽车工艺】汽车车身激光焊工艺
【汽车工艺】挤压铸造铝合金转向节开发
【汽车工艺】焊接速度对车身激光 -MIG 复合焊接的影响
【汽车工艺】储能模组pack生产线总览
【汽车工艺】汽车总装工艺的设计原则与总体布局
【汽车工艺】汽车总装工艺技术应用及发展趋势探讨
【汽车工艺】汽车车身常见工艺孔的类型、功能及设计原则
【汽车工艺】高性能铝合金汽车底盘型材的生产工艺
【汽车工艺】汽车底盘装配生产工艺
↓↓↓
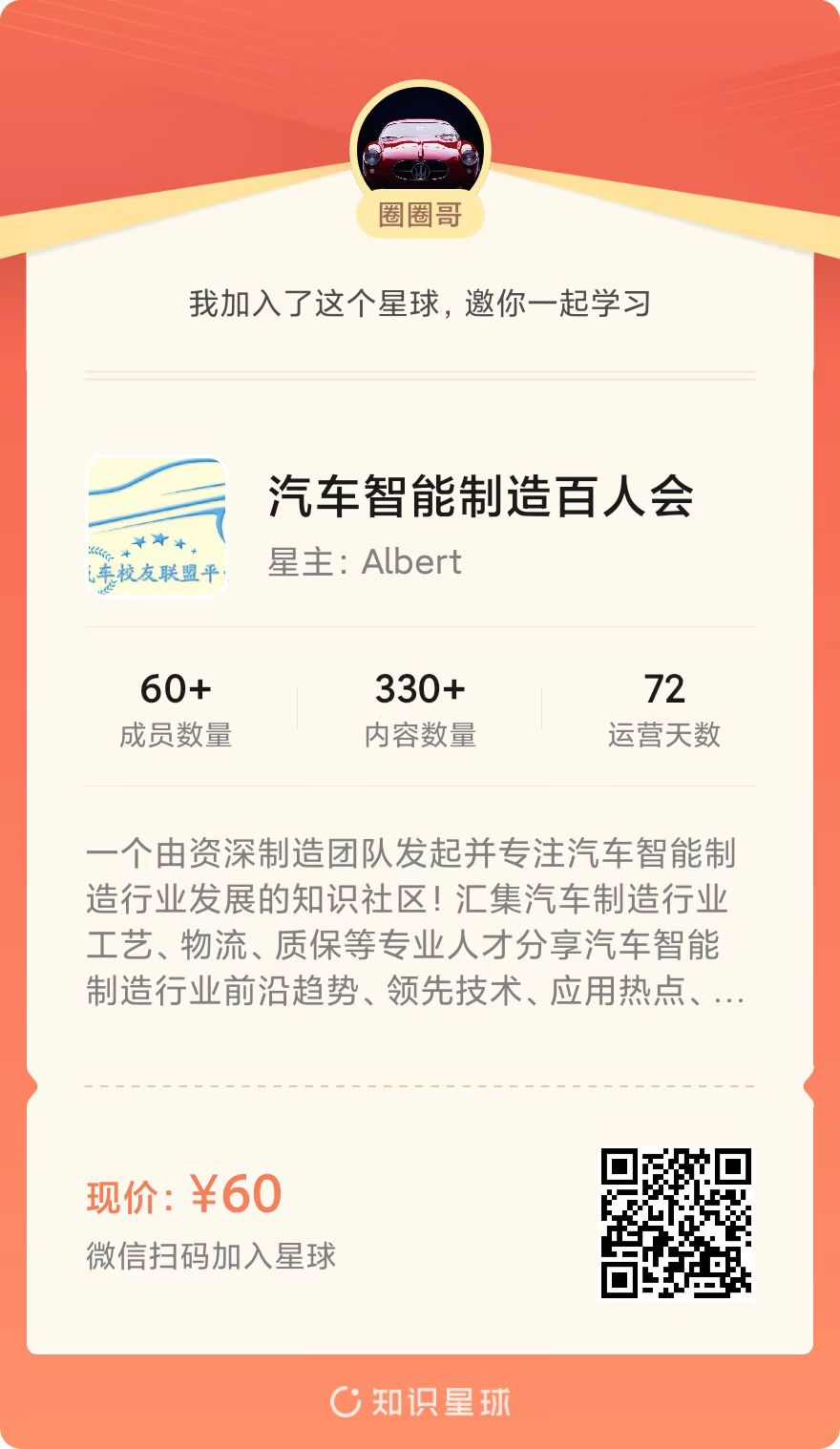
一个由资深制造团队发起并专注,汽车智能制造行业发展的知识社区!汇集汽车制造行业工艺、物流、质保等专业人才分享汽车智能制造行业前沿趋势、领先技术、应用热点、典型案例和实施策略 ,推动汽车制造业向数字化、网联化、智能化、共享化发展。3天可自由退款,无广告,只干货!如需进入智能制造微信群(智能制造、四大工艺、新能源三电工艺等)请添加群管理员automan2023
摘 要:随着汽车行业的不断发展和消费者质量意识的不断提升,车身防腐性能成为汽车企业竞争力的重要要素之一。为了降低新车型开发成本,缩短开发周期,车身防腐性能提升应从涂装SE阶段开始。本文主要介绍了汽车涂装SE阶段防腐性分析的主要内容,同时对典型问题进行探讨分析,结合经验提出优化建议,提高新产品的防腐性能。汽车使用过程中,白车身防腐性能优劣对汽车使用寿命影响重大。研究表明,车身锈蚀1%,其强度就降低5%~10%。一般来说,除意外交通事故外,腐蚀是汽车损坏和报废常见的重要原因。而随着消费者质量意识的提高,车身防腐性能也成为企业竞争力的重要要素之一。车身防腐性能与车身结构、材料及工艺等息息相关。在涂装SE阶段,车身防腐性分析主要是从电泳通电性、排气性、排水性、涂胶注蜡工艺等方面对白车身数模进行审核,识别可能影响白车身防腐性能的车身结构和不合理的涂胶注蜡工艺设计,及时提出设计变更,对提升车身防腐性能,降低新车型研发成本,具有重要的工程应用意义。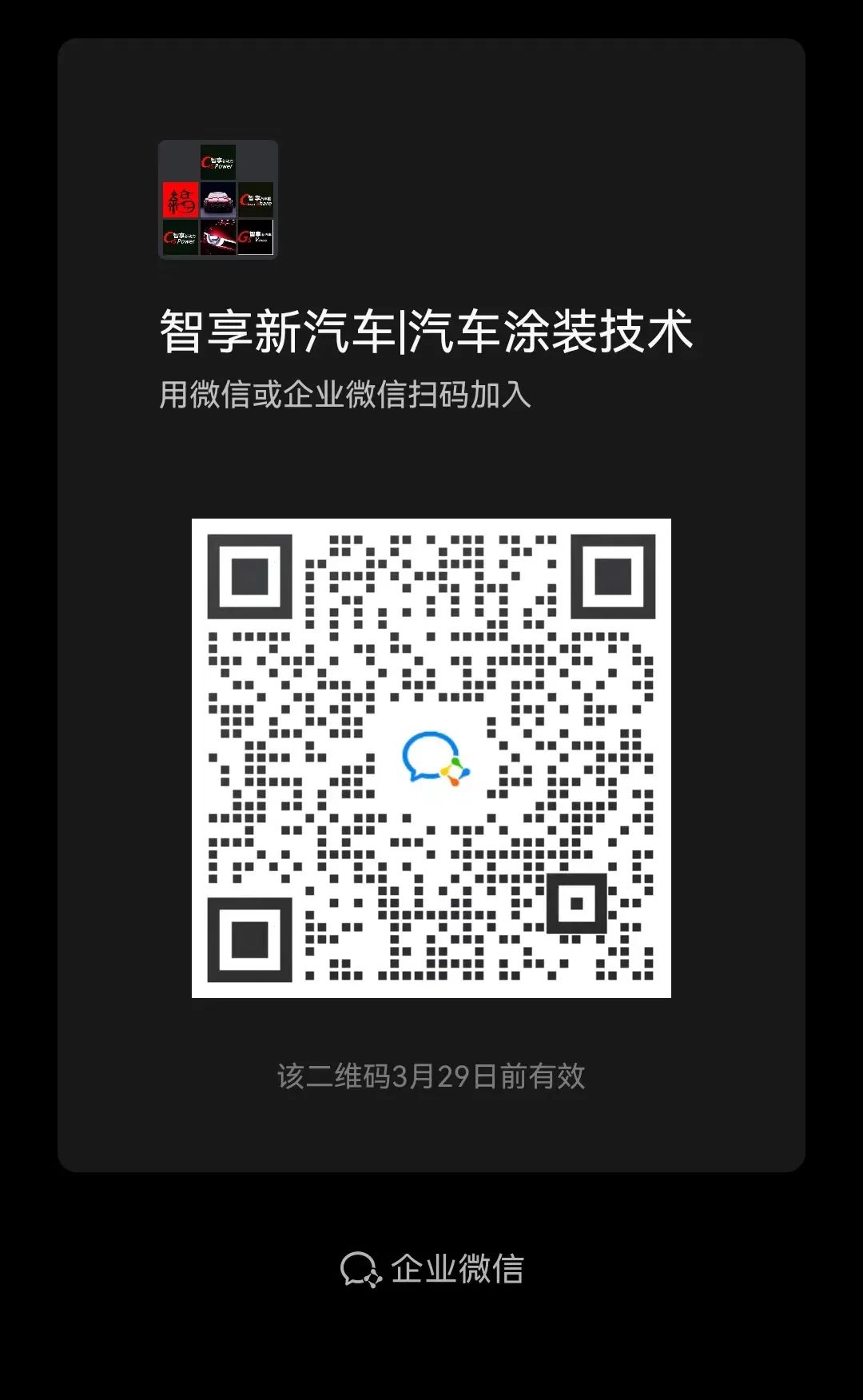
目前汽车主要采用阴极电泳涂装方式。阴极电泳涂装是将白车身作为阴极,浸渍在充满电泳涂料的槽体中,在电泳槽两侧及底部布置与车身对应的阳极,电泳时在两极之间通电,使白车身表面及内腔析出均匀、水不溶涂膜的涂装方法。由于车身钣金结构复杂,会对电泳电场产生屏蔽作用,导致车身内腔电泳涂膜厚度偏低,甚至出现完全未能电泳的情况。因此在涂装SE阶段需要对白车身结构进行审核,对电场屏蔽部位提出相应的设计变更。1.1 侧围电泳通电性分析
由于侧围属于侧碰安全防护的重要部位,侧围大部分位置均采用三层钣金结构加强,电泳涂装时电场屏蔽严重,如A立柱、B立柱及侧围上边梁等区域,均属于电泳薄弱部位。如图1,A立柱上部区域,侧围外蒙皮、A立柱加强板与A立柱内板形成典型的三层钣金结构。一方面,侧围外蒙皮属于车身外观大件,不能设置电泳通电孔,电场仅能通过侧围A立柱内板和A立柱加强板进入内腔①中,电场通过困难。另一方面,侧围外蒙皮与A立柱加强板之间间隙仅8.3mm,电场通过A立柱加强板后,辐射范围较小,侧围外蒙皮及A立柱加强板可能会出现电泳不良,甚至未电泳情况,严重影响车身防腐性能和车身强度。在A立柱加强板上间隔150~200mm设置大小为12*30mm的电泳通电孔,如图2。电泳涂装时,电场通过增加的电泳孔进入腔体①中,消除电场屏蔽。后期电泳车身拆解结果表明,经过加孔后的A立柱加强板及侧围外蒙皮内板电泳良好。1.2 纵梁电泳通电性
车身纵梁在汽车使用过程中,所处位置较低,涉水几率大,处于白车身“湿区”,使用环境恶劣,属于防腐关重部位。例如,纵梁中段总成的纵梁中段、纵梁中段内加强板、纵梁中段前加强板和前地板四层钣金形成封闭空腔(见图3),设计时易出现电泳通电孔设置不足或各层钣金间电泳孔错孔布置情况,电泳涂装时电场进入困难,导致纵梁内腔电泳膜厚偏低,防腐性能较差。如图4,纵梁中段、纵梁中段内加强板及纵梁中段前加强板间隔不大于200mm设置φ20mm的电泳通电贯通孔(可借用纵梁上焊装定位孔),并将纵梁中段与纵梁中段内加强板之间的间隙调整到不小于5mm,使电泳槽液流动顺畅,确保纵梁各个内腔电泳良好,提高车身防腐性能。若纵梁外板被车身其他结构件遮挡,无法在外板上设置电泳孔时,可在纵梁侧面或车内地板面上对应位置设置电泳通电孔。在车内地板面上设置电泳孔时,由于车内电场较车外电场偏弱,根据经验电泳孔直径按Φ30mm布置,如图5。1.3 门槛电泳通电性
门槛与纵梁类似,由于位置较低,涉水几率较高,也属于涂装电泳防腐关重部位。图6为门槛内腔电泳电场线模拟示意图,根据经验,门槛电泳孔按下列条件布置:①门槛外板按照200mm~250mm设置φ20mm的电泳通电孔;②门槛加强件按照200mm设置φ20mm的电泳通电孔;③门槛内板按照200mm设置φ20mm的电泳通电孔;④前端和后端第一个电泳通电孔按距离边界不大于100mm设置。电泳涂装时,由于输送方式不同,车身进出电泳槽体的角度、在槽内运动姿态有着较大的区别。目前涂装前处理输送方式主要有间歇式、双摆杆全浸式(图7-①)及Rodip-3 360°旋转全浸式(图7-②)。间歇式(垂直进出)和双摆杆输送(进出槽角度 30 °~45 °)由于进出槽角度限制,电泳涂装时车身局部位置会存在气体无法排出的情况,形成“气室”,导致该区域电泳漆膜偏薄,甚至完全未电泳情况发生,防腐能力较差。在涂装SE阶段,需根据生产线输送方式对车身排气不良部位提出相应的设计变更。例如,车身右侧后轮毂包因加油管路布置的缘故,顶部结构部分凸起,如图8。此结构在电泳涂装前处理使用间歇式及双摆杆全浸式输送方式时,顶部形成“气室”,电泳时电泳涂料无法在此区域沉积析出,导致该区域电泳不良。电泳涂装时,为将轮毂包内气体排出,需要在最高点位置设置排气结构。通常设置凸筋结构来排气,如图9。排气筋高度一般为2mm~3mm,排气筋宽度根据实际结构确定,以既能保证顺利排气,又不影响后续密封为原则。另外需注意在焊接车间涂覆焊装点焊密封胶时不能堵住此排气筋,避免在电泳时失去排气作用。白车身电泳排水性是指在白车身从出槽到进入下一工序前的这段时间内,车身结构的沥液性能。一般的判断标准是进入下一工序前不应有连续的工艺液体流出。电泳排水性不佳,一方面会使上一工序槽液未沥干进入到下一工序槽体中,出现“串槽”现象,导致槽液污染;另一方面会因槽液未沥干,导致电泳车身烘干时,形成“电泳斑”(白色斑痕,电泳膜厚较低)缺陷,防腐性能降低。而车身排水性能主要与车身漏液孔大小、数量及车身结构有关,在涂装SE阶段需对其进行校核,对不利于漏液的车身结构提出相应的设计变更。地板漏液一般采用φ30mm的圆孔,且设置在吊具状态下最低点位置,如图10。根据经验,漏液孔数量可以通过漏液孔总面积与前后地板面积比值和相同生产线生产的成熟车型对比来确定,具体计算如下:经过验证表明,新车型M值与该线体生产的成熟车型M值相当时,车身能在规定时间内漏液完全,从而计算出新车型漏液孔数量n。白车身中一些容易导致积液的典型钣金结构,也需要在涂装SE阶段进行规避。如图11,车身前地板加强筋结构设计导致地板上形成局部凹槽,容易导致积液。数据校核时应变更为图示中凸筋结构,使液体能顺利流散并通过地板漏液孔排出。另外前、后门及背门下部也需要设置漏液孔来保证其排水性。如图12,根据经验,漏液孔应按如下条件设置:①漏液孔应按200mm~400mm间距设置;②为避免注包边密封胶时与漏液孔干涉,漏液孔下边缘距离包边边缘距离≥5mm;③为保证门盖件漏液完全,漏液孔下边缘应位于门内板R角以下或与之齐平,若结构不允许情况下,漏液孔高于R角下边缘时,漏液孔下边缘距离R角距离≤1.5mm。受车身结构及阴极电泳工艺限制,车身总存在电泳涂膜较为薄弱部位,如钣金贴合、间隙较小钣金搭接部位及钣金边止口边位置等;还有一些车身在使用过程中受到外部环境破坏,导致防腐性能降低部位,如经常受到石子冲击的底盘及轮毂包区域。这些区域需要通过涂胶及注蜡工艺对防腐性能进行弥补。4.1 涂胶
车身涂装涂胶主要分为焊接密封胶、PVC抗石击胶两种。在涂装SE阶段,除需设置具有密封功能的焊缝密封胶外,对间隙较小的钣金搭接部位需增加焊缝密封胶涂覆,防止杂质及水汽进入其中对钣金产生腐蚀。另外由于电泳工艺局限,钣金止口边电泳漆膜普遍偏薄,存在锐边锈蚀现象,因此处于湿热环境中的前机舱内钣金边缘也需增加焊缝密封胶涂覆,提高其防腐性能。为保护底盘及轮毂包内电泳涂膜在使用过程中不受石子冲击破坏,涂装时涂覆PVC抗石击胶对电泳涂膜进行保护。在涂装SE阶段,PVC抗石击胶的涂覆部位应按照总装装配后,底盘及轮毂包区域钣金外露部分确定。4.2 注蜡
研究表明,有空腔石蜡涂覆的电泳涂膜钣金比仅有电泳涂膜涂覆的钣金耐锈穿能力提高2~3年。防腐目标较高的汽车厂,常会采用注空腔石蜡方式来提高车身防腐性能。空腔石蜡一般设置在电泳漆膜薄弱和使用环境较为恶劣区域,如五门一罩内外板包边缝隙和底盘区域部分梁上,一些高档汽车底盘所有梁均要求注蜡。在涂装SE阶段,需根据生产线注蜡设备的具体情况及车身防腐要求,校核注蜡孔尺寸、数量和注蜡操作性。在新车型数据设计阶段通过涂装SE分析,预先对可能出现的问题进行有效处理,降低新车型的开发成本,缩短产品的开发周期,对提高车身涂装质量有着重要意义。而防腐性分析是涂装SE分析中一个比较重要的环节,通过车身涂装电泳通电性、排气性、排水性及涂胶注蜡工艺分析,提高车身防腐性能,延长汽车使用寿命,从而达到提升车身品质和市场竞争力的目的。说明:来源汽车科技,由干货小Q整理,转载请注明出处【车新材料】,如涉及版权等问题,请您告知,我们将及时处理。如需申请内外饰、车身、座椅等专业群请添加微信GSAuto0001验证信息后要求进群。
免费投稿请发送邮件到:gearshare@163.com
(欢迎行业内人士踊跃投稿,将你们的文章分享给大家)
▼加入智享汽车圈知识星球,获取汽车行业海量干货