
群:如需申请内外饰、车身、座椅、智能制造等专业群请添加微信GSAuto0001验证信息后要求进群。
征稿:关于汽车新材料、新工艺、新技术的文稿,请发送至gearshare@163.com
社群推荐:GSAuto联盟|座椅技术专家委员会招新了
热门推荐:
【汽车工艺】汽车制造中多种焊接方法大总结,就一个字,全!【汽车设计】主流汽车零部件产品开发项目管理方法对比【汽车工艺】16家车企揭示的中国汽车制造工业4.0现状(内附评估模型)【汽车工艺】各种焊接技术知识汇总,20分钟全搞定!【汽车工艺】汽车轻量化高端汽车铝合金冲压板材的应用【汽车设计】车载动力电池包的有限元分析及轻量化设计【汽车工艺】焊接工艺问题及解决措施
【汽车工艺】焊接质量控制,这些内容SQE要掌握
【汽车设计】纯电动乘用车动力电池包整车布置集成研究【汽车工艺】从1—10的一体化压铸:投产元年
【汽车工艺】特斯拉压铸工艺解析
【汽车工艺】特斯拉车身材料及工艺解析
【汽车工艺】模具行业专题研究:大型一体压铸的技术核心
【汽车工艺】汽车铝合金车身连接工艺方法大全
【汽车工艺】全铝车身结构与材料应用及连接工艺剖析(奥迪、蔚来汽车、奇瑞捷豹路虎、通用凯迪拉克)
【汽车工艺】汽车总装工艺的总体布局
【汽车工艺】焊装车间——车身工艺流程介绍
【汽车工艺】不同铸造工艺对产品结构的影响
【汽车工艺】纯电动汽车与传统汽车总装工艺对比分析
【汽车工艺】低成本汽车车身试制夹具的敏捷开发
【汽车工艺】汽车总装工艺流程的设计
【汽车工艺】一种3mm厚汽车热成形产品
【汽车工艺】汽车车身激光焊工艺
↓↓↓
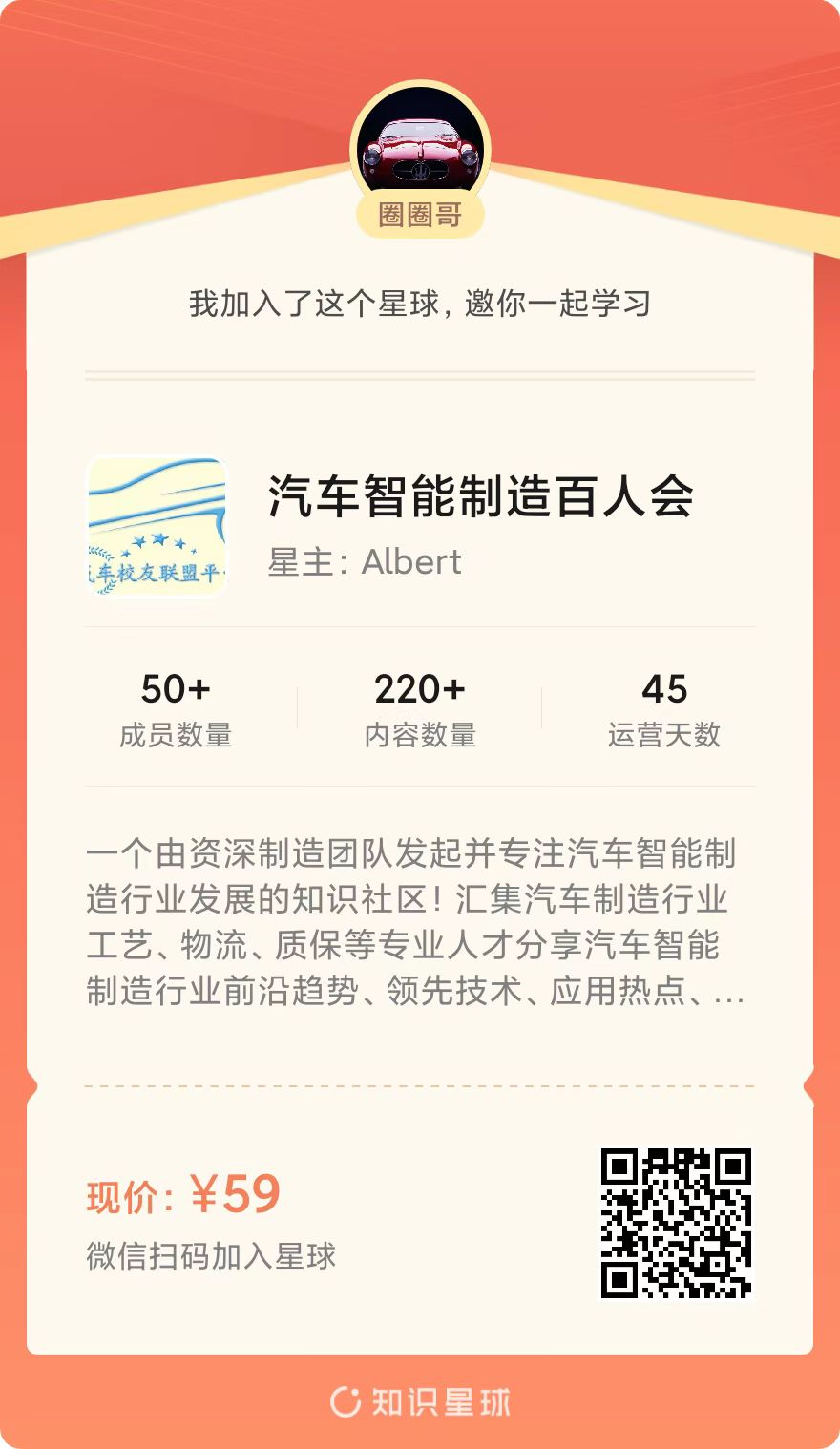
一个由资深制造团队发起并专注,汽车智能制造行业发展的知识社区!汇集汽车制造行业工艺、物流、质保等专业人才分享汽车智能制造行业前沿趋势、领先技术、应用热点、典型案例和实施策略 ,推动汽车制造业向数字化、网联化、智能化、共享化发展。3天可自由退款,无广告,只干货!如需进入智能制造微信群(智能制造、四大工艺、新能源三电工艺等)请添加群管理员automan2023
摘 要:采用铝合金挤压铸造间接挤压工艺代替球铁生产转向节,结合结构优化设计,使转向节质量降低了56.6%,轻量化效果显著。开发过程采用模拟计算与实际试验相结合的方法,得到的铸件组织和力学性能优良,且静力破坏试验、耐久试验指标均满足使用要求。随着环保要求的提高、汽车市场竞争加剧,汽车轻量化是大势所趋,铝合金在汽车底盘上的应用呈现快速发展态势,如控制臂类、摆臂类、连杆类、轮边支架类等底盘件已部分应用铝合金制造[1],在高端豪华车型中,甚至出现了铝合金底盘部件的高度集成应用。挤压铸造工艺可消除铸件内部缩孔、缩松等缺陷,铸件组织致密,并可通过热处理进一步提高力学性能,性能接近锻件水平,是一种具有广阔应用前景的精确成形工艺[2]。转向节属于底盘安全件,具有连接、承载、转向功能,服役条件复杂。本课题转向节原型搭载在某SUV车型,生产工艺为球墨铸铁砂型铸造,质量为4.5kg,采用挤压铸造工艺制造铝合金转向节,结合结构优化,可满足铸件性能要求,且减重效果明显,符合环保发展要求。
原球铁转向节形状复杂,所用材料牌号为QTA,强度较高,屈服强度不小于275MPa,铸件见图1。以此为原型,保证与环境件(前轮、减震器、转向拉杆、三角臂)接口及硬点不变,初始结构模型见图2,其中转向节与三角臂球销连接处更改为锥形孔结构。采用挤压铸造工艺生产A356合金转向节,经T6热处理后屈服强度和抗拉强度分别可达240MPa和320MPa,伸长率为10%[3],本课题中铸件经结构优化、工艺优化后,挤压铸造铝合金转向节可替代铸铁转向节。 根据CAE模拟结果优化结构,经过几轮优化,最终得到铝合金转向节优化模型见图3,质量为2.19kg,减重比例达56.6%。8种典型工况下转向节的应力云图、位移云图分别见图4和图5。应力模拟最大值见表1。可以看出,8种工况下的最大应力均满足要求,小于A356合金的屈服强度。对最终转向节模型采用路谱输入进行耐久性能仿真分析,原球铁转向节与铝合金转向节的最大损伤值及损伤分布情况对比见表2。分析结果表明,铝合金转向节耐久性能与原球铁转向节相当。转向节采用宇部HVSC-800PL卧式挤压铸造机生产,在模具设计上采用间接挤压铸造工艺布置。对铝合金转向节挤压铸造工艺进行前期模拟分析,基本参数见表3。前期模拟发现,凝固过程中最后的液相区在零件前轮中心中部偏下,在此处也存在热节,易出现缩孔或缩松缺陷。为保证充型平稳及补缩良好,中间与轮毂单元连接的圆孔部位进行填实处理,结合水冷+局部挤压进行改善,转向节上部水冷通道布置见图6,挤压杆布置及效果见图7,增压参数和局部挤压参数见表4。
转向节充型过程模拟结果见图8。可见金属液从压室进入料饼,平稳上升,首先填充转向节三角臂连接臂侧,依次进入制动钳安装孔部位、转向拉杆连接臂,最后上升进入并填充满减震器连接臂处。整个充型过程中铝液自底向上逐步充满整个模具型腔,无卷气现象发生。结合水冷与局部挤压效果的凝固过程模拟结果见图9。经过局部挤压后,铸件孤立液相区集中在中部区域,见图9d,该部位会在后期加工去除。对转向节进行T6热处理,热处理制度为530℃×480min固溶处理+40℃水冷+180℃×360min时效处理。在热处理过程中发现铸件减震器安装孔出现大量气泡,分析发现涂料喷涂该处一定模次后堵塞了排气槽。将该处排气槽深度打磨到0.5mm,并在每20模次后肉眼检查排气槽堵塞情况或观察铸件排气槽余料的厚度进行预防。对铸件进行X射线探伤及剖切检查,发现减震器安装孔厚大处存在1级缩松,铸件局部挤压部位存在一定厚度的预料,发现该处局部挤压没有发生作用。通过加大挤压杆配合间隙到单边80~100μm,缺陷消除。经改进后的试制工艺出品率为53%,废品率为10%。从改进后的铝合金转向节上取样,对试样进行力学性能检测。在铝合金转向节上典型位置取拉伸试样进行测试,取样位置及编号见图10。其力学性能检测结果见表5,结果能够达到预期要求。
图11为转向节金相组织。可以看出,合金组织为α相+颗粒状共晶Si+少量针状Fe相,未见缩孔、缩松等缺陷,有轻微偏析。用XG16042L/C X射线成像系统对试制的转向节逐件进行X射线探伤,见图12。按ASTM-E155标准,该铸件符合内部缺陷等级≤2级的技术要求。对铝合金转向节加工并装配后,模拟整车状态安装在试验工装上,试验加载力的大小、方向、加载频率等均与原球铁转向节相同,加载点在轮胎中心与地面接触点处。采用SCHENCK 160kN/100mm 液压伺服试验设备,其中耐久试验频率为5Hz,进行规定次数的循环加载后观察试样状态。对转向节进行典型工况的静强度及耐久台架试验后,铸件均未出现裂纹、变形、损坏等状况。将铝合金转向节搭载在整车上,在某试验场通过了8万公里耐久试验。
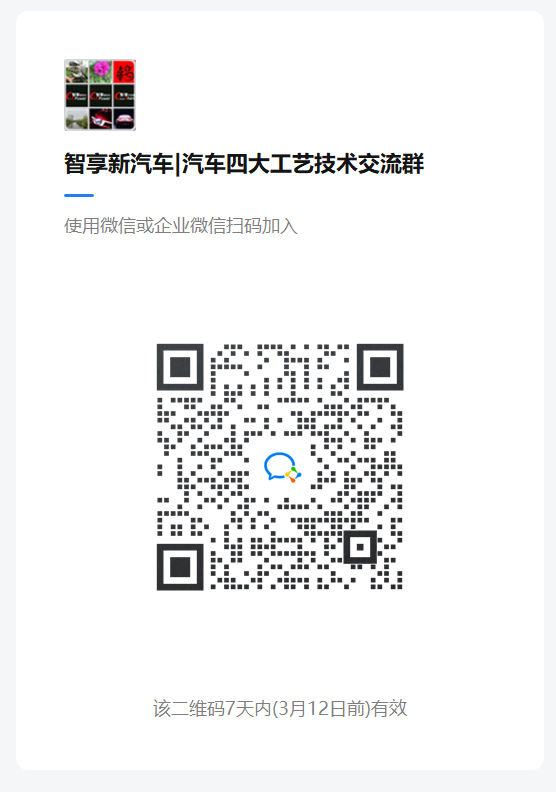
转向节生产工艺由球墨铸铁砂型铸造改为铝合金间接挤压铸造,结合结构优化设计,质量由4.5kg减至2.19kg,减重达56.6%,轻量化效果显著。结合水冷设计和局部挤压设计,挤压铸造工艺得到的铸件的组织和力学性能优良,静力破坏试验、耐久试验均满足使用要求,具有良好的应用前景。说明:来源希骥车身与附件,由干货小Q整理,转载请注明出处【车新材料】,如涉及版权等问题,请您告知,我们将及时处理。如需申请内外饰、车身、座椅等专业群请添加微信GSAuto0001验证信息后要求进群。
免费投稿请发送邮件到:gearshare@163.com
(欢迎行业内人士踊跃投稿,将你们的文章分享给大家)
▼加入智享汽车圈知识星球,获取汽车行业海量干货