
群:如需申请内外饰、车身、座椅、智能制造等专业群请添加微信GSAuto0001验证信息后要求进群。
征稿:关于汽车新材料、新工艺、新技术的文稿,请发送至gearshare@163.com
社群推荐:GSAuto联盟|座椅技术专家委员会招新了
热门推荐:
【汽车工艺】汽车制造中多种焊接方法大总结,就一个字,全!【汽车设计】主流汽车零部件产品开发项目管理方法对比【汽车工艺】16家车企揭示的中国汽车制造工业4.0现状(内附评估模型)【汽车工艺】各种焊接技术知识汇总,20分钟全搞定!【汽车工艺】汽车轻量化高端汽车铝合金冲压板材的应用【汽车设计】车载动力电池包的有限元分析及轻量化设计【汽车工艺】焊接工艺问题及解决措施
【汽车工艺】焊接质量控制,这些内容SQE要掌握
【汽车设计】纯电动乘用车动力电池包整车布置集成研究【汽车工艺】从1—10的一体化压铸:投产元年
【汽车工艺】特斯拉压铸工艺解析
【汽车工艺】特斯拉车身材料及工艺解析
【汽车工艺】模具行业专题研究:大型一体压铸的技术核心
【汽车工艺】汽车铝合金车身连接工艺方法大全
【汽车工艺】全铝车身结构与材料应用及连接工艺剖析(奥迪、蔚来汽车、奇瑞捷豹路虎、通用凯迪拉克)
【汽车工艺】汽车总装工艺的总体布局
【汽车工艺】焊装车间——车身工艺流程介绍
【汽车工艺】不同铸造工艺对产品结构的影响
【汽车工艺】纯电动汽车与传统汽车总装工艺对比分析
【汽车工艺】低成本汽车车身试制夹具的敏捷开发
↓↓↓
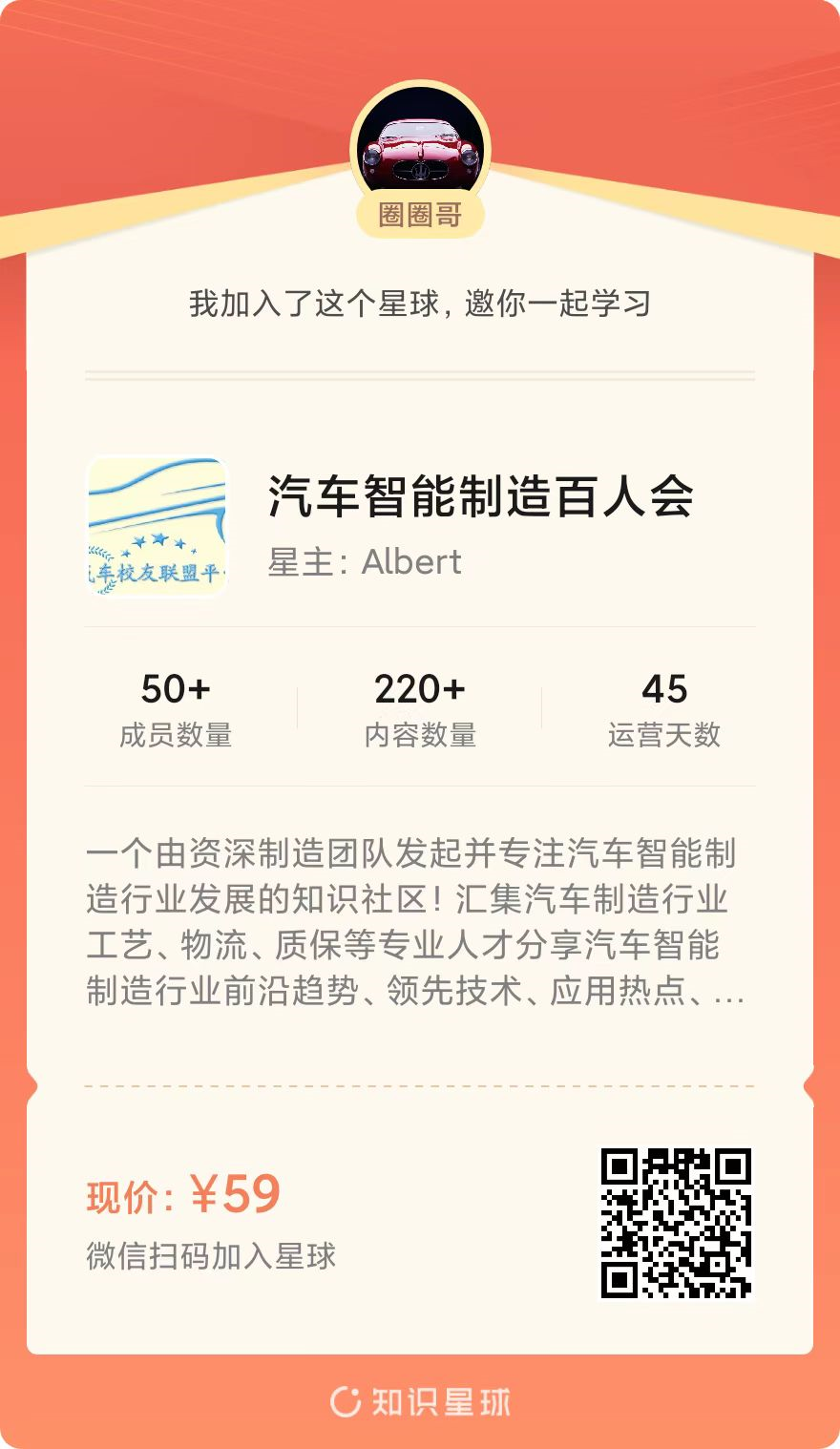
一个由资深制造团队发起并专注,汽车智能制造行业发展的知识社区!汇集汽车制造行业工艺、物流、质保等专业人才分享汽车智能制造行业前沿趋势、领先技术、应用热点、典型案例和实施策略 ,推动汽车制造业向数字化、网联化、智能化、共享化发展。3天可自由退款,无广告,只干货!如需进入智能制造微信群(智能制造、四大工艺、新能源三电工艺等)请添加群管理员automan2023
汽车总装工艺作业流程主要分为内外饰线、底盘线、最终线、分装线、检测线及终检线。总装工艺流程设计需要考虑生产线通过性(如空间、设备、工装及安全等方面)、产线布局(如工位数量、工位节距、节拍及仿真技术等)及工艺技术(如装配特性、扭矩、加注及工艺设备水平等)三方面。合理的工艺流程设计可以在控制成本的前提下,使产线具有更好的柔性和适应性,进而决定着汽车制造商的生产能力、产品质量、成本控制及工艺技术水平等。随着制造工艺技术的发展,汽车总装工艺流程的设计向着自动化、模块化、平台化、标准化、智能化及人性化的趋势发展,这也是企业快速响应市场,提高竞争力和降低生产成本的战略选择。W——工时总额(汽车从上线到下线的装配总时间),min;T——生产节拍(从生产线下线 1 台整车需要的时间),min/台;d——工位密度(每个工位上的平均人数),人/工位,一般取值为2~3人/工位;JPH——单位小时生产数量(在生产线不间断的情况下每小时生产汽车的数量,是衡量1条生产线的产能高低能力的重要指标),台/h;μ——生产线设备开动率,也是作为衡量生产线工作效率的指标,一般生产线开动率取值为 90%~95%;L——工位节距(每个工位在生产线所占的长度),m;两车间距——主要考虑装配操作的安全性和便利性,一般设定在1.2~1.5m。
1)工序集中原则:将多车型的相同操作集中在相同工位,尽量使用相同工具,这样不仅减少设备投资,也减少装配工时,提高生产效率。2)工序分散原则:汽车生产是处于一个价值流下的流水线。为了生产线工时平衡,需将许多小件和独立的装配内容分散到多个工位上,平衡工位间的工时差。同时应具有防错和复检功能,提高产品质量。3)多车型混线的基本原则:采用 RPS 定位系统共用。车身定位基准是汽车生产的总定位点,因此作为车身各子总成在整车身的工艺基准,保持车身坐标系一致性是生产输送线的基本原则。焊装、涂装及总装车间输送的定位基准和装配工艺基准,如图1所示。工艺流程设计要参考企业生产车型的复杂程度,如车型的产品特点、档次、零部件模块化程度、生产线工艺水平及工艺技术能力等因素;零部件总成彼此装配关系和产品技术条件;生产纲领和节拍要求;法规限制和企业资源能力等;形成最优的工艺流程,从而达到车间工位数量最少,缩短生产线的长度,减少总装车间的面积,提高生产线的柔性化和可扩展性能力。汽车总装生产线主要分为内外饰线、底盘线、最终线及分装线。工序排布要参考生产线的布局特点,根据整车物料清单(BOM)表信息,按照结构特点将整车各系统合理分布到各段生产线,再以零部件总成为单位合理编排到各工位。根据各零部件的装配关联性和产品属性层级合理设定装配逻辑顺序。一般按照串联或并联的装配属性、上下先后顺序及由内至外的覆盖层级进行逐层覆盖性装配,同时考虑避免工序作业干扰,以及预留检验工序。混线生产中,将各车型的相同零件总成布置到相同的工位上装配,例如前后悬架和前后保险杠等。将系统零件安排在同一工位进行集中装配,提高装配效率,起到很好的防错和物流便利性,避免错漏装发生和利于质量控制。考虑到装配人员操作空间的舒适性,工位密度一般以 2~3 人/工位的密度值为佳。如图 2 所示,工位人员布置主要由汽车左右两侧、前后及内外组合排列构成。原则是装配工序互相没有干涉及行走路程无重叠区域;避免相邻汽车的前汽车背门区域与后汽车的前舱区域同时布置人员;避免同汽车的两侧和车体内同时布置人员。一般是同工位汽车两侧布置人员装配对称性零部件;同工位布置前舱区域和后舱区域人员;同工位布置车体内区域与前舱区域或背门区域人员。再根据车型特点综合排布。部分独立工序为了保证装配质量,从物料配送及生产安全角度考虑,通常不会与其他工序关联,该工位不宜规划其他装配内容,基本原则是占用独立工位来完成。比如前后风挡的涂胶和装配工序,轮胎安装和拧紧工序,汽车燃油加注工序,底盘和车身合装工序,整车四轮定位工序等。一般大型设备在工艺流程设计之初就要优先设定和考虑,以减少工艺流程的变更和修改对大型设备的影响。比如前后风挡玻璃涂胶设备一般布置在内饰线体的最后工位,内饰线的工艺流程做何种变化也不会造成影响。底盘合车工序一般布置在底盘线中后段,给予足够的缓冲工位来应对突发事件,确保整车性能的重要工艺装配质量。油液加注设备一般集中优先布置在最终线处,优先采用多合一形式的油液加注设备。力矩是总装工艺中最重要的工艺质量参数之一,尽量采用高精度拧紧设备。工艺流程原则上尽量设计为:同一工位上1名员工只使用1种拧紧工具进行1种力矩值或同种规格螺栓的多个标准件拧紧作业。减少套筒更换工序,不允许1名人员使用超过2种拧紧设备。对于1把高精度伺服电动拧紧工具需要拧紧不同规格和力矩值的作业,必须增加防错和记数等追溯功能装置。结合生产车型的标准件类型、数量及力矩值大小,需要考虑工序内标准件力矩和对边尺寸的统一。在不影响产品性能的前提下,将工艺力矩进行整合,从而达到减少标准件种类,减少使用工具种类的目的,将装配达到最佳的简量化。尽量采用模块化技术装配,汽车总装模块化生产可以显著缩短生产线长度、降低总装工艺复杂性、缩小工厂规模及提高生产线柔性化。例如在没有采用模块化的情况下,装配冷凝器、散热器、防撞梁、前组合灯总成及机盖锁等工序内容至少需要6个工位,采用前端化技术装配,只需要1个工位就可以完成前端模块的装配,显著减少工位长度和装配难度。目前可实现的总装模块化主要有前端模块化、车门模块化、底盘模块化、顶棚集成化、油箱集成化、IP模块化及车轮模块化等。总装装配内容主要是由人完成装配,故零部件的装配便利性要与作业人员动作姿势匹配,以人员站姿装配为佳,尽量避免装配人员过高、弯曲及侧身的动作,以减少对人员的职业健康伤害。对于底盘线的作业流程,建议采用高度可调和车身可旋转 90°的C型钳吊具来提高底盘装配人机性;对于内饰线的作业流程,经常出现人员装配位置和车身悬挂高度不吻合,作业人员需要用下蹲或身体弯曲的姿势来完成装配作业。通过采用 z 向高度柔性可调的车身托盘,可以保证在不同的工位将车身定位在合理的高度,方便人员站立式装配,减少下蹲及弯曲躯干造成的身体机能劳损。对于其他过重或大件的零部件,采用助力机械手辅助装配,以减少作业人员的劳动量和劳动强度。考虑在线维修和生产掉线的突发情况,对于装配关系存在先后串联属性的较大零部件,至少隔开1个延迟工位进行排布。比如天窗与顶棚的装配关系为先后串联属性,虽然必须先装配天窗总成后才能装配顶棚,但是在工艺流程设计时,一般要求顶棚总成与天窗总成至少错开1个工位的延迟距离,是为了预防天窗装配出现质量问题或装配人员跟不上生产节拍掉线,留给响应人员在线处理问题的时间。易燃、易爆、易碎及有毒物质或零部件的装配尽量放在生产线后端工位,以减少安全防护工作量。如汽油加注设备工位一般布置在生产线后端工位区域,按消防要求该工位应与厂房通道大门距离最短且畅行无阻。考虑工艺技术的进步和企业的战略发展。工艺流程设计之初,要预留一部分的扩展工位,以满足后续平台车型的增加,以及混线生产造成的工艺流程变更,以便在后续车型上线装配时,不至于出现工位长度不足导致的现场装配拥挤现象。生产线均衡的目的是在满足约束的状态下使特定目标函数最大化或最小化。目前普遍认为总装工艺流程平衡性的问题主要分为3大类:1) 生产纲领确定了生产节拍大小,求最少生产线工位的问题;2)生产纲领确定了生产线工位数量,求最小生产节拍的问题;3)生产线工位数和生产节拍都确定了的情况下,求混线车型之间生产的负荷均衡性问题。优化生产线平衡的方法主要有5M法,即:从人、 机、料、法、环5个环节入手改善;以及 ECRS法,即:取消(Eliminate)、合并(Combine)、重排(Rearrang)及简化(Simply),从改善作业手法角度上优化生产线平衡。多品种混线的生产线和通用设备占总设备的比例,是评价混流生产线经济性与柔性化能力的重要指标。1)对于发动机分装及合车的工装设备,必须设计成柔性化通用工装,以满足多个不同动力配置的装配;2)对于仪表总成、前端模块及车门模块等的助力机械手,尽量采用通用的夹持孔和定位销,以达到一套助力机械手满足不同车型的装配需求;3)不同车型的各种油液加注口设计上要保持一致,才能满足加注设备的共用;4)标准件规格及对边尺寸尽量采用国标产品,减少非标设计,以达到减少拧紧工具种类,减少设备采购费用的目的。从价值流的理念出发,工艺流程设计目标函数是在一定节拍条件下使各工位非增值时间总和最小或增值时间总和最大。物流配送过程不增加增值属性或任何附加值,因此物流运输距离要短,搬运量要小。尽量采用 SPS 物流模式,减少人员走动时间及物料搬运时间。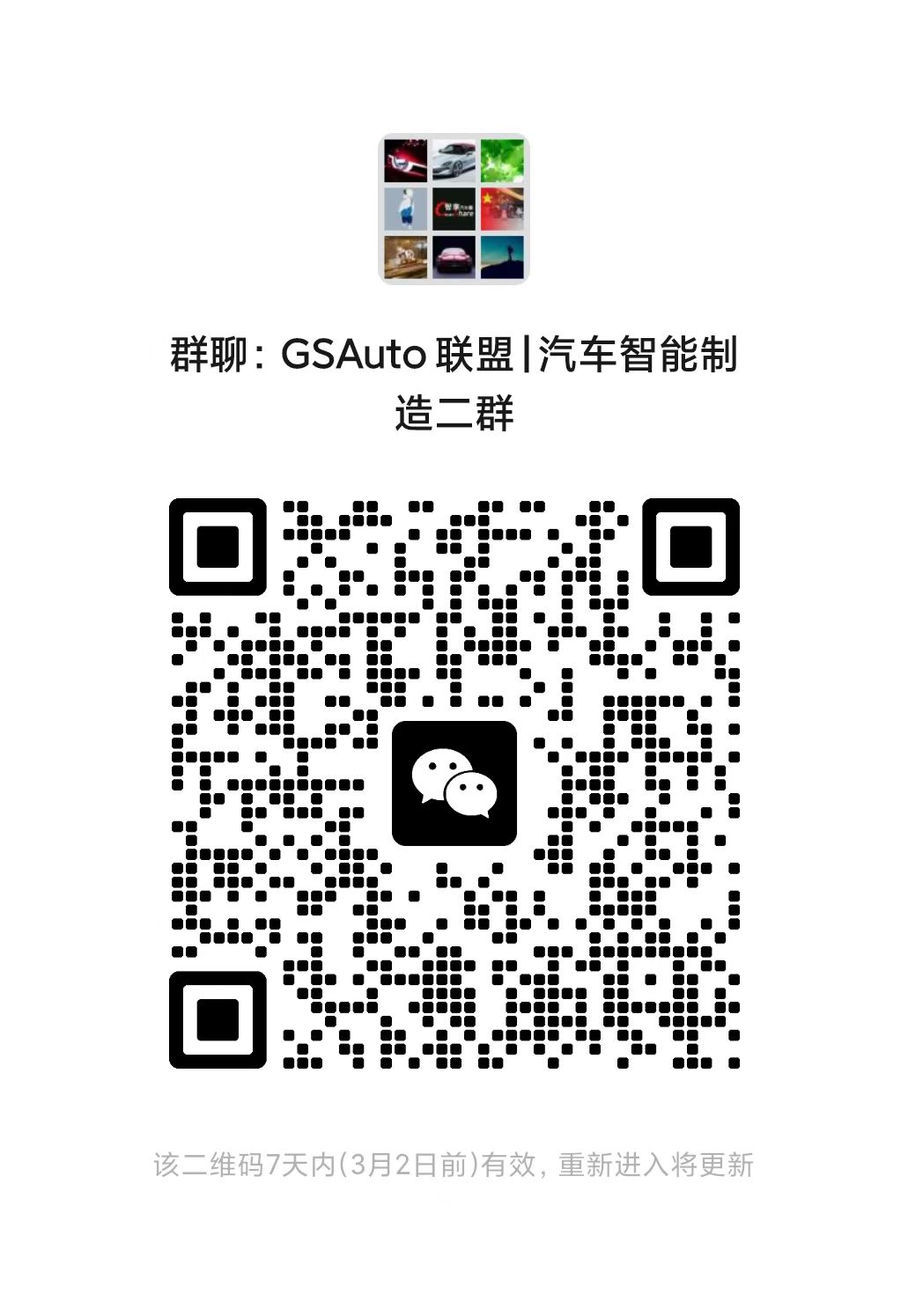
说明:来源旺材汽车轻量化,由干货小Q整理,转载请注明出处【车新材料】,如涉及版权等问题,请您告知,我们将及时处理。如需申请内外饰、车身、座椅等专业群请添加微信GSAuto0001验证信息后要求进群。
免费投稿请发送邮件到:gearshare@163.com
(欢迎行业内人士踊跃投稿,将你们的文章分享给大家)
▼加入智享汽车圈知识星球,获取汽车行业海量干货