石墨类负极是主流,但提升空间有限
负极材料是锂电池四大关键材料之一,约占整个锂电池制造成本8%左右,关键用在于可逆地脱/嵌锂离子,是由活性物质、粘结剂和添加剂制成糊状胶合剂后,涂抹在铜箔两侧,经过干燥、压制而成。目前锂离子电池负极材料以石墨类为主。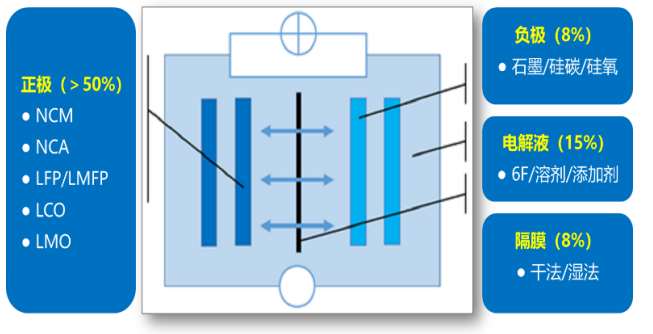
图1 锂电池成本构成
负极比容量的增加对电池比容量提升效果显著,寻找新一代负极材料正当其时。锂电池的质量能量密度主要由正极克容量、负极克容量以及正负极电势差决定。实验室测试显示,电池比容量随着正极材料比容量的上升而显著提高,而在正极材料比容量一定的条件下,负极材料比容量对电池的比容量的提升并非线性关系,在负极材料300mAh/g~1200mAh/g 阶段,电池比容量提升效果显著。随正极三元材料高镍化趋势正盛,提升负极材料质量比容量的重要性与日俱增。
目前主流厂商的石墨负极产品比容量均在350mAh/g 以上,接近理论比容量上限 372mAh/g,寻找更高
比容量的新型负极材料正当其时。
快充技术的发展需要电芯材料的革新相匹配。快充技术也是锂电池技术进步的方向,
石墨材料由于其层状结构决定锂离子必须从材料的端面嵌入,然后扩散至颗粒内部,致使传输路径较长,嵌锂过程较慢限制了锂离子电池的快充应用,同时其对锂电位过低也致使在大电流充电过程中发生锂沉积副反应造成析锂,析出的锂金属以枝晶的形
式生长,有可能会刺穿隔膜,危害电池安全。
硅基负极比容量极高、快充优,但体积膨胀、导电性较弱
硅基负极材料的机制与石墨不同,通过合金和去合金化反应进行,在已知的负极材料中,拥有的理论比容量高达4200mAh/g,是石墨材料的10倍以上,并且硅能从各个方向提供锂离子嵌入和脱出的通道,快充性能优异,同时其对锂电位 略高于石墨也较好的解决了析锂难题。
硅作为负极材料在实际应用中存在首次库伦效率低、倍率性能和循环性能差等问题。尽管硅具备相当可观的嵌锂容量,但在嵌锂过程中将会出现严重的体积膨胀和结构变化。体积膨胀产生的机械应力不断破坏硅颗粒表面的SEI膜,多次循环最终导致锂离子消耗殆尽,循环性能变差;在现有电解液中,锂盐LiPF6分解产生的微量HF也会对硅造成腐蚀,导致硅负极的容量发生衰减,使得电池的首次库伦效率偏低;由于硅是半导体材料,电子电导率和离子电导率低影响其电级反应速率,使得倍率性能变低。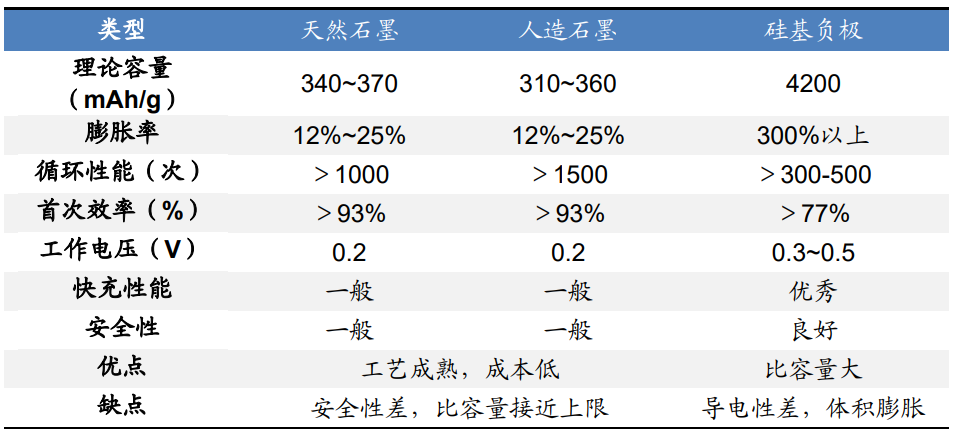
图2 负极材料性能对比
硅碳与硅氧是主流方向,技术创新空间巨大
由于单质硅的体积膨胀系数过大,因此在实际的商业应用中,硅负极主要采用掺杂的方式加入到人造石墨中,主流技术路线为硅碳和硅氧,硅碳负极是指纳米硅与石墨材料混合,硅氧负极则采用氧化亚硅与石墨材料复合。在硅与不同材料的复合过程中,通常会结合结构设计(纳米化和多孔硅)等辅助工艺手段提供膨胀空间,硅基材料在复合材料中主要作为活性物质提供容量,其他材料作为载体,缓冲体积膨胀。此外,硅基负极材料会设计成包覆结构,最外层用碳包覆来充当导电网络,也可避免电解液直接接触硅基材料发生副反应。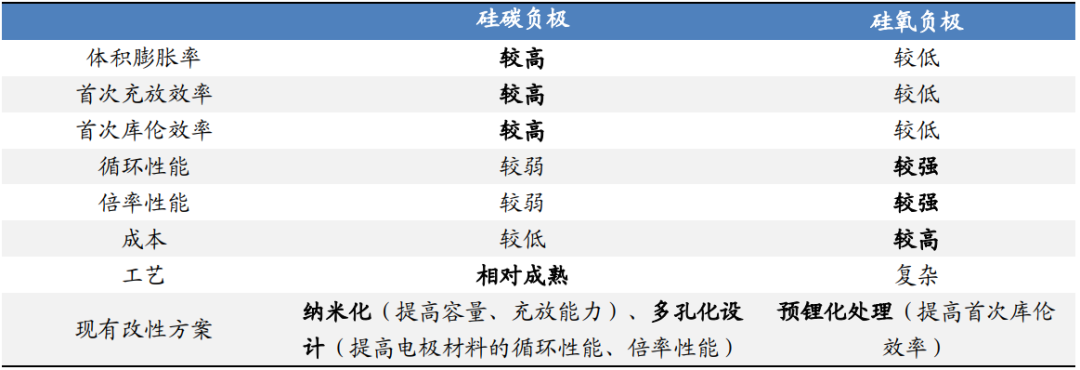
图3 硅碳负极和硅氧负极性能对比
从制备方式上看,主要用到的技术手段有机械球磨法、化学气相沉积法、高温热解法、溶胶凝胶法,其中机械球磨和化学气相沉积法对设备要求较为简单,制造成本较低,
在工业化量产中更为主流。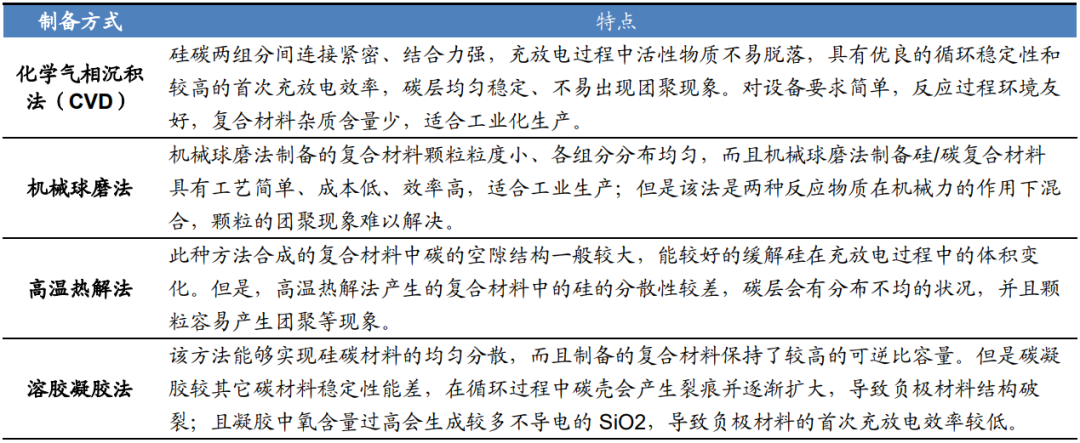
图4 主要硅基负极制备流程中的主要方式
在硅碳负极的制备过程中,需要首先制备纳米硅颗粒,最外层由碳做包覆层,形成壳核结构。目前硅碳负极的商业化容量在450mAh/g以下,首效高但体积膨胀较大,因此其循环性能相对较差。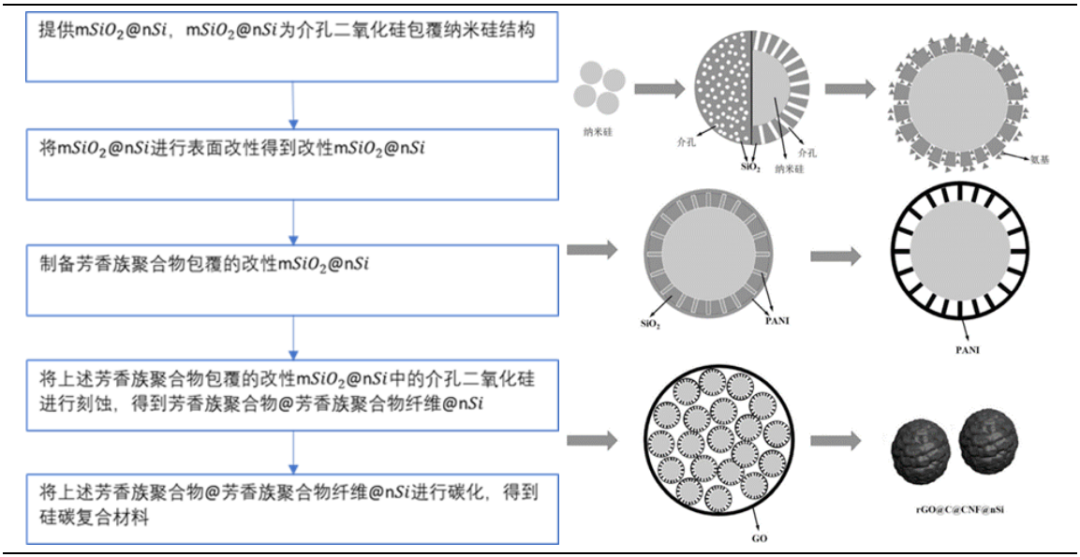
图5 贝特瑞的一种硅碳负极制备工艺
硅氧负极首效低,成本高,但循环性能更好。硅氧负极的制备过程并不唯一,通常是先制备锂离子电池用氧化亚硅,然后进行碳包覆等后续工艺。但传统制备氧化亚硅的生产效率低且结构难控制,紫宸新材料提出一种直接将Si、 SiO2和还原性金属按比例混和,省去了制备氧化亚硅的流程,得到一种有混合晶相的硅氧负极材料。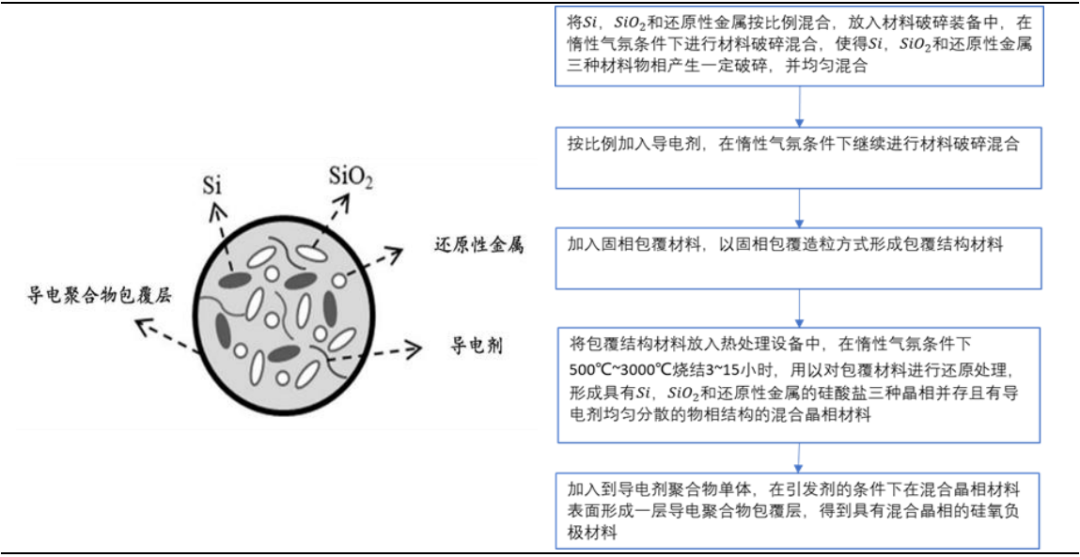
图6 溧阳紫宸新材料的硅氧负极制备工艺
工艺,研发,机理和专利!软包电池方向重磅汇总资料分享!
搞懂锂电池阻抗谱(EIS)不容易,这篇综述值得一看!锂电池循环寿命研究汇总(附60份精品资料免费下载)