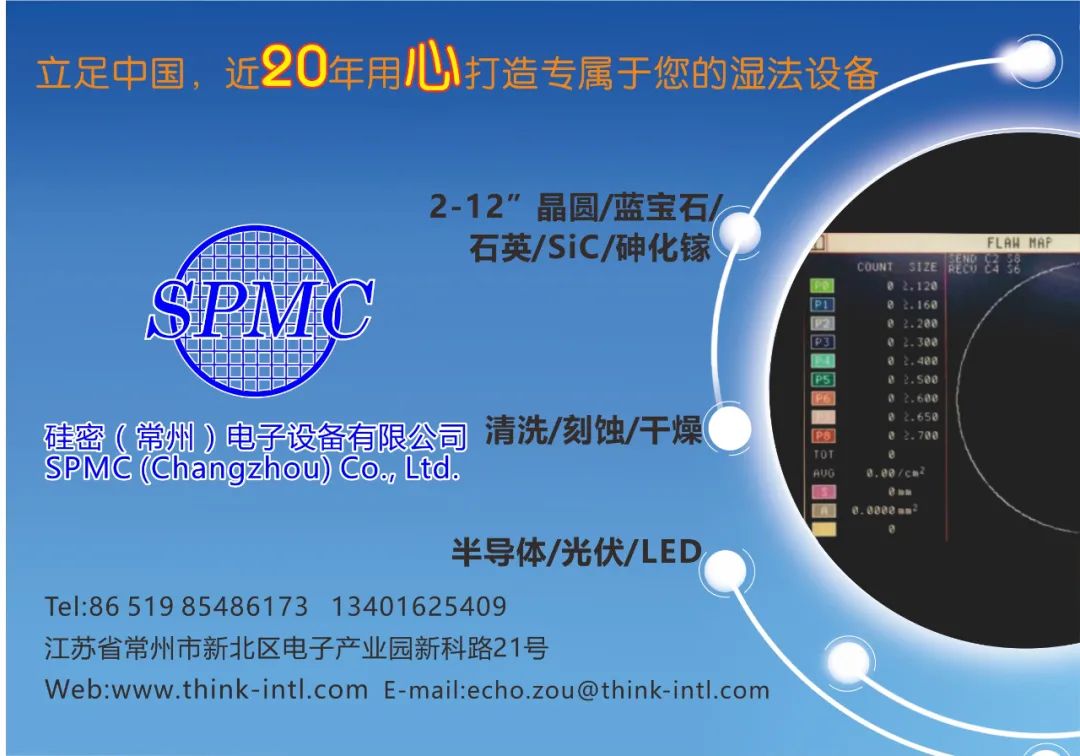
*免责声明:转载仅为了传达一种不同的观点,不代表今日半导体对该观点赞同或支持,内容如有侵权,请联系本部删除!手机微信同15800497114。
碳化硅(SiC)材料是功率半导体行业主要进步发展方向,用于制作功率器件,可显着提高电能利用率。可预见的未来内,新能源汽车是碳化硅功率器件的主要应用场景。特斯拉作为技术先驱,已率先在Model 3中集成全碳化硅模块,其他一线车企亦皆计划扩大碳化硅的应用。随着碳化硅器件制造成本的日渐降低、工艺技术的逐步成熟,碳化硅功率器件行业未来可期。碳化硅(SiC)是第三代化合物半导体材料。半导体产业的基石是芯片,制作芯片的核心材料按照历史进程分为:第一代半导体材料(大部分为目前广泛使用的高纯度硅),第二代化合物半导体材料(砷化镓、磷化铟),第三代化合物半导体材料(碳化硅、氮化镓) 。碳化硅因其优越的物理性能:高禁带宽度(对应高击穿电场和高功率密度)、高电导率、高热导率,将是未来最被广泛使用的制作半导体芯片的基础材料。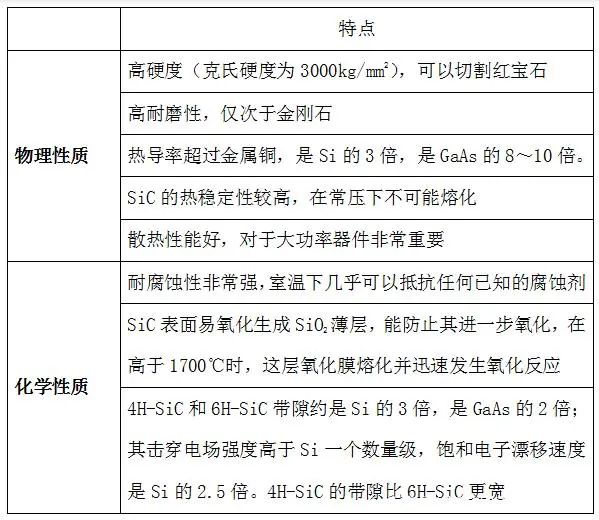
碳化硅在半导体芯片中的主要形式为衬底。半导体芯片分为集成电路和分立器件,但不论是集成电路还是分立器件,其基本结构都可划分为“衬底-外延-器件” 结构。碳化硅在半导体中存在的主要形式是作为衬底材料。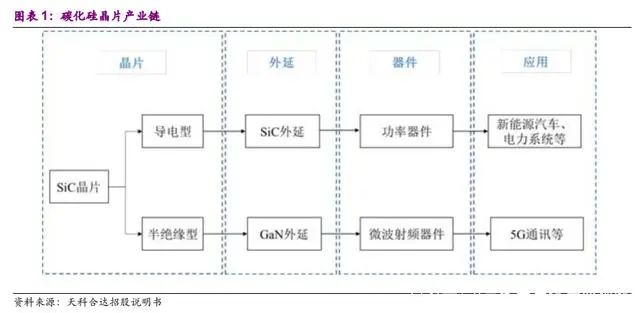
碳化硅晶片是碳化硅晶体经过切割、研磨、抛光、清洗等工序加工形成的单晶薄片。碳化硅晶片作为半导体衬底材料,经过外延生长、器件制造等环节,可制成碳化硅基功率器件和微波射频器件,是第三代半导体产业发展的重要基础材料。根据电阻率不同,碳化硅晶片可分为导电型和半绝缘型。其中,导电型碳化硅晶片主要应用于制造耐高温、耐高压的功率器件,市场规模较大;半绝缘型碳化硅衬底主要应用于微波射频器件等领域,随着 5G 通讯网络的加速建设,市场需求提升较为明显。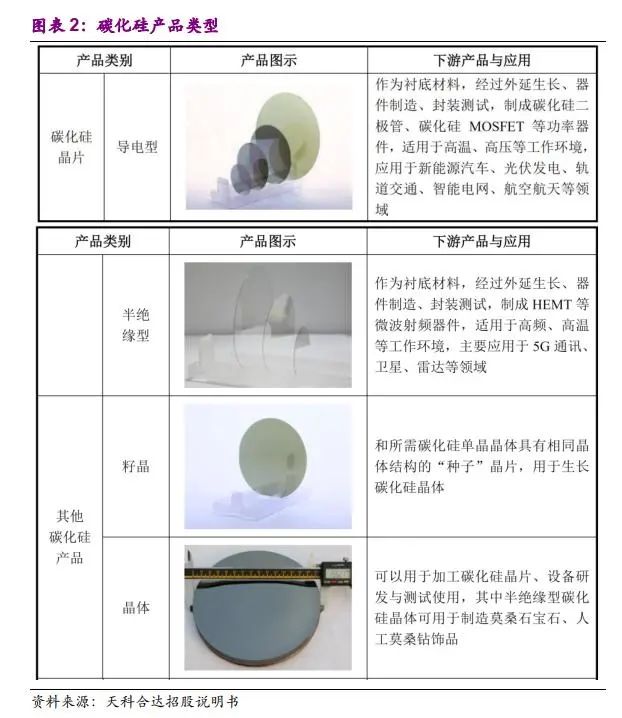
SiC的硬度仅次于金刚石,可以作为砂轮等磨具的磨料,因此对其进行机械加工主要是利用金刚石砂轮磨削、研磨和抛光,其中金刚石砂轮磨削加工的效率最高,是加工SiC的重要手段。但是SiC材料不仅具有高硬度的特点,高脆性、低断裂韧性也使得其磨削加工过程中易引起材料的脆性断裂从而在材料表面留下表面破碎层,且产生较为严重的表面与亚表层损伤,影响加工精度。因此,深入研究SiC磨削机理与亚表面损伤对于提高SiC磨削加工效率和表面质量具有重要意义。对硬脆材料进行研磨,磨料对其具有滚轧作用或微切削作用。磨粒作用于有凹凸和裂纹的表面上时,随着研磨加工的进行,在研磨载荷的作用下,部分磨粒被压入工件,并用露出的尖端划刻工件的表面进行微切削加工。另一部分磨粒在工件和研磨盘之间进行滚动而产生滚轧作用,使工件的表面形成微裂纹,裂纹延伸使工件表面形成脆性碎裂的切屑,从而达到表面去除的目的。因为硬脆材料的抗拉强度比抗压强度要小,对磨粒施加载荷时,会在硬脆材料表面的拉伸应力的最大处产生微裂纹。当纵横交错的裂纹延伸且相互交叉时,受裂纹包围的部分就会破碎并崩离出小碎块。此为硬脆材料研磨时的切屑生成和表面形成的基本过程。由于碳化硅材料属于高硬脆性材料,需要采用专用的研磨液,碳化硅研磨的主要技术难点在于高硬度材料减薄厚度的精确测量及控制,磨削后晶圆表面出现损伤、微裂纹和残余应力,碳化硅晶圆减薄后会产生比碳化硅晶圆更大的翘曲现象。目前碳化硅的抛光方法主要有:机械抛光、磁流变抛光、化学机械抛光(CMP)、电化学抛光(ECMP)、催化剂辅助抛光或催化辅助刻蚀(CACP/CARE)、摩擦化学抛光(TCP,又称无磨料抛光)和等离子辅助抛光(PAP)等。化学机械抛光(CMP)技术是目前半导体加工的重要手段,也是目前能将单晶硅表面加工到原子级光滑最有效的工艺方法,是能在加工过程中同时实现局部和全局平坦化的唯一实用技术。CMP的加工效率主要由工件表面的化学反应速率决定。通过研究工艺参数对SiC材料抛光速率的影响,结果表明:旋转速率和抛光压力的影响较大;温度和抛光液pH值的影响不大。为提高材料的抛光速率应尽量提高转速,虽然增加抛光压力也可提高去除速率,但容易损坏抛光垫。目前的碳化硅抛光方法存在着材料去除率低、成本高的问题,且无磨粒研抛、催化辅助加工等加工方法,由于要求的条件苛刻、装置操作复杂,目前仍处在实验室范围内,批量生产的实现可能性不大。人类1905年 第一次在陨石中发现碳化硅,现在主要来源于人工合成,碳化硅有许多用途,行业跨度大,可用于单晶硅、多晶硅、砷化钾、石英晶体等、太阳能光伏产业、半导体产业、压电晶体产业工程性加工材料。碳化硅晶片是以高纯硅粉和高纯碳粉作为原材料,采用物理气相传输法(PVT) 生长碳化硅晶体,加工制成碳化硅晶片。①原料合成。将高纯硅粉和高纯碳粉按一定配比混合,在 2,000℃以上的高温下反应合成碳化硅颗粒。再经过破碎、清洗等工序,制得满足晶体生长要求的高纯度碳化硅微粉原料。②晶体生长。以高纯度碳化硅微粉为原料,使用自主研制的晶体生长炉,采用物理气相传输法(PVT 法)生长碳化硅晶体。其生长原理如下图所示: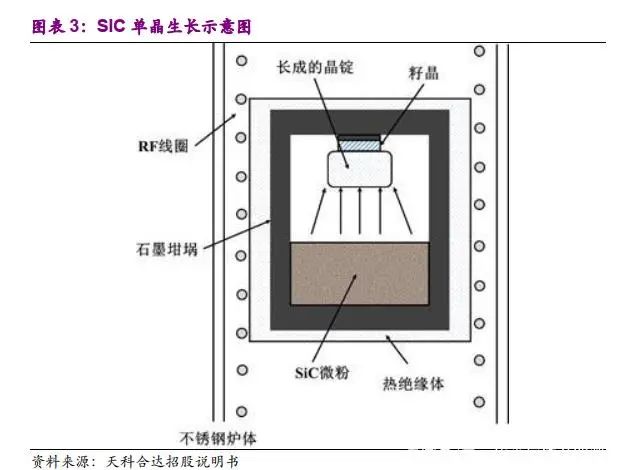
将高纯碳化硅微粉和籽晶分别置于单晶生长炉内圆柱状密闭的石墨坩埚下部和顶部,通过电磁感应将坩埚加热至 2,000℃以上,控制籽晶处温度略低于下部微粉处,在坩埚内形成轴向温度梯度。碳化硅微粉在高温下升华形成气相的 Si2C、 SiC2、 Si 等物质,在温度梯度驱动下到达温度较低的籽晶处,并在其上结晶形成圆柱状碳化硅晶锭。③晶锭加工。将制得的碳化硅晶锭使用 X 射线单晶定向仪进行定向,之后磨平、滚磨,加工成标准直径尺寸的碳化硅晶体。④晶体切割。使用多线切割设备,将碳化硅晶体切割成厚度不超过 1mm 的薄片。⑤晶片研磨。通过不同颗粒粒径的金刚石研磨液将晶片研磨到所需的平整度和粗糙度。⑥晶片抛光。通过机械抛光和化学机械抛光方法得到表面无损伤的碳化硅抛光片。⑦晶片检测。使用光学显微镜、 X 射线衍射仪、原子力显微镜、非接触电阻率测试仪、表面平整度测试仪、表面缺陷综合测试仪等仪器设备,检测碳化硅晶片的微管密度、结晶质量、表面粗糙度、电阻率、翘曲度、弯曲度、厚度变化、表面划痕等各项参数指标,据此判定晶片的质量等级。⑧晶片清洗。以清洗药剂和纯水对碳化硅抛光片进行清洗处理,去除抛光片上残留的抛光液等表面沾污物,再通过超高纯氮气和甩干机将晶片吹干、甩干;将晶片在超净室封装在洁净片盒内,形成可供下游即开即用的碳化硅晶片。晶片尺寸越大,对应晶体的生长与加工技术难度越大,而下游器件的制造效率越高、单位成本越低。目前国际碳化硅晶片厂商主要提供 4 英寸至 6英寸碳化硅晶片, CREE、 II-VI 等国际龙头企业已开始投资建设 8 英寸碳化硅晶片生产线。
此处为广告,与本文内容无关
硅是半导体行业第一代基础材料,目前全球95%以上的集成电路元器件是以硅为衬底制造的。目前,随着电动汽车、5G等应用的发展,高功率、耐高压、高频率器件需求快速增长。当电压大于900V,要实现更大功率时,硅基功率MOSFET和IGBT就暴露出短板,其在转换效率,开关频率,工作温度等多方面都将受限。而碳化硅(SiC)材料由于具有禁带宽度大(Si的3倍)、热导率高(Si的3.3倍或GaAs的10倍)、电子饱和迁移速率高(Si的2.5倍)和击穿电场高(Si的10倍或GaAs的5倍)等性质,SiC器件在高温、高压、高频、大功率电子器件领域和航天、军工、核能等极端环境应用领域有着不可替代的优势,弥补了传统半导体材料器件在实际应用中的缺陷,正逐渐成为功率半导体的主流。碳化硅是用石英砂、石油焦(或煤焦)、木屑(生产绿色碳化硅时需要加食盐)等原料通过电阻炉高温冶炼而成。第三代半导体,由于在物理结构上具有能级禁带宽的特点,又称为宽禁带半导体,主要是以氮化镓和碳化硅为代表,其在半导体性能特征上与第一代的硅、第二代的砷化镓有所区别,使得其能够具备高禁带宽度、高热导率、高击穿场强、高电子饱和漂移速率等优势,从而能够开发出更适应高温、高功率、高压、高频以及抗辐射等恶劣条件的小型化功率半导体器件,可有效突破传统硅基功率半导体器件及其材料的物理极限。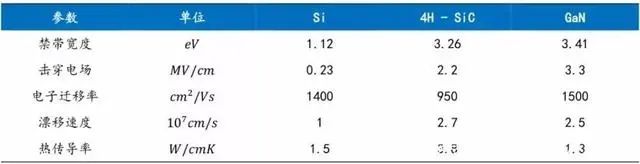
资料来源:Semikron – Application Manual Power Semicondu整体来看,碳化硅的耐高压能力是硅的10倍、耐高温能力是硅的2倍、高频能力是硅的2倍,与硅基模块相比,碳化硅二极管及开关管组成的模块(全碳模块),不仅具有碳化硅材料本征特性优势,还可以缩小模块体积50%以上、消减电子转换损耗80%以上,从而降低综合成本。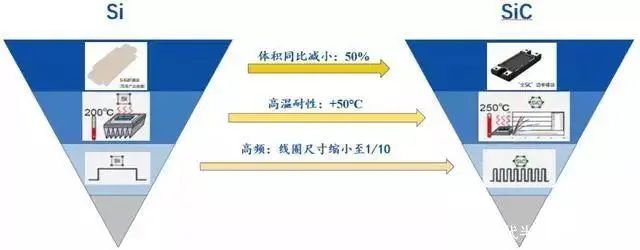
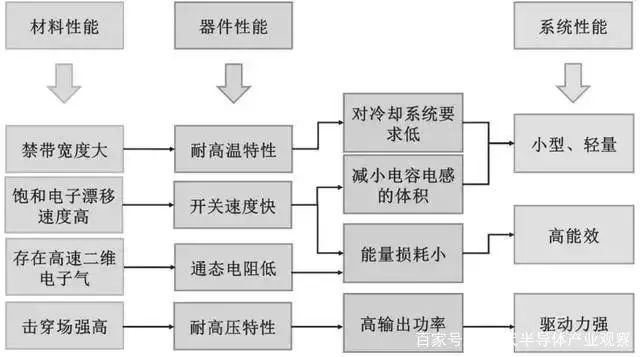
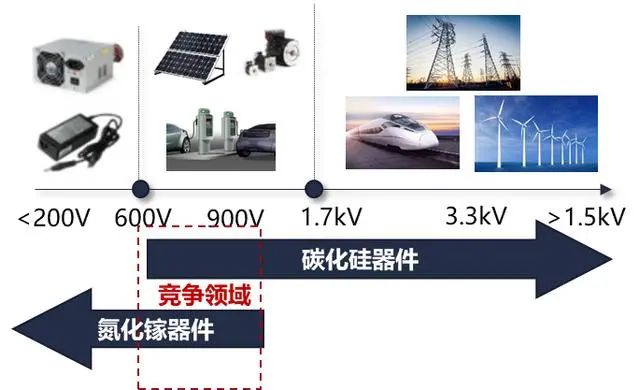
数据来源:第三代半导体产业技术创新战略联盟《第三代半导体电力电子技术路线图》通信电源是服务器、基站通讯的能源库,为各种传输设备提供电能,保证通讯系统正常运行。碳化硅MOSFET的高频特性使得电源电路中的磁性单元体积更小、重量更轻,电源整体效率更高;碳化硅肖特基二极管反向恢复几乎为零的特性使其在许多PFC电路中具有广阔的应用前景。例如,在3kW高效通信电源无桥交错PFC电路中,使用650V/10A碳化硅肖特基二极管,可以帮助客户实现满载效率大于等于95%的高技术要求。新能源汽车行业的快速发展带动了充电柱的需求增长,对新能源电动汽车而言,提升充电速度和降低充电成本是行业发展的两大目标。在充电桩电源模块中使用碳化硅器件,可以实现充电桩电源模块的高效化和高功率化,进而实现充电速度的提升和充电成本的降低。服务器电源是服务器能源库,服务器提供电能,保证服务器系统正常运行。在服务器电源中使用碳化硅功率器件,可以提升服务器电源的功率密度和效率,整体上缩小数据中心的体积,实现数据中心整体建设成本的降低,同时实现更高的环保效率。例如,在3kW服务器电源模块中,在图腾柱PFC中使用碳化硅MOSFET可以显着提升服务器电源的效率,实现更高的效率要求。特高压作为大型系统工程,将催发从原材料和元器件等一系列的需求,而功率器件是输电端特高压直流输电中FACTS柔性输电技术和变电端电力电子变压器(PET)的关键器件。直流断路器作为柔性直流输电的关键部分之一,其可靠性对整个输电系统的稳定性有着较大影响。使用传统硅基器件设计直流断路器需要多级子单元串联,在直流断路器中使用高电压碳化硅器件可以大大减少串联子单元数量,是行业研究的重点方向。5. 城际高铁和城际轨道交通——牵引变流器、电力电子变压器、辅助变流器、辅助电源未来轨道交通对电力电子装置,比如牵引变流器、电力电子电压器等提出了更高的要求。采用碳化硅功率器件可以大幅度提高这些装置的功率密度和工作效率,将有助于明显减轻轨道交通的载重系统。碳化硅器件可以实现设备进一步高效率化和小型化,在轨道交通方面具有巨大的技术优势。日本新干线N700S已经率先在牵引变流器中使用碳化硅功率器件,大幅降低整车的重量,实现更高的运载效率和降低运营成本。根据YoleDéveloppement的数据,2018年全球SiC器件市场规模为4.2亿美元,2019年规模增长至5.64亿美元。未来,随着电动汽车、动力电池,以及电力供应和太阳能的发展,SiC器件市场将进一步快速增长,特别是电动汽车及动力电池的驱动。预计2024年,全球SiC器件市场规模将增长至20亿美元,2018至2024年期间的复合增长率接近30%。根据Yole预测,2020年SiC器件市场规模仍有增长,预计在2023年随着电动汽车的崛起开始快速增长。据IHS数据,2023年全球SiC器件需求有望达16.44亿美元,2017-2023年复合增速约为26.6%;下游主要应用场景包含EV、快充桩、UPS电源(通信)、光伏、轨交以及航天军工等领域,其中电动车行业有望迎来快速爆发(CAGR81.4%),通信、光伏等市场空间较大。伴随SiC器件成本下降,全生命周期成本性能优势有望不断放大,潜在替代空间巨大。先进半导体材料已上升至国家战略层面,2025年目标渗透率超过50%。底层材料与技术是半导体发展的基础科学,在2025中国制造中,分别对第三代半导体单晶衬底、光电子器件/模块、电力电子器件/模块、射频器件/模块等细分领域做出了目标规划。在任务目标中提到2025实现在5G通信、高效能源管理中的国产化率达到50%;在新能源汽车、消费电子中实现规模应用,在通用照明市场渗透率达到80%以上。从产业格局看,目前全球SiC产业格局呈现美国、欧洲、日本三足鼎立态势。其中美国全球独大,占有全球SiC产量的70%~80%,碳化硅晶圆市场CREE一家市占率高达6成之多;欧洲拥有完整的SiC衬底、外延、器件以及应用产业链,在全球电力电子市场拥有强大的话语权;日本是设备和模块开发方面的绝对领先者。SiC功率器件的制备过程,包含SiC粉末合成、单晶生长、晶片切磨抛、外延(镀膜)、前道工艺(芯片制备)、后道封装。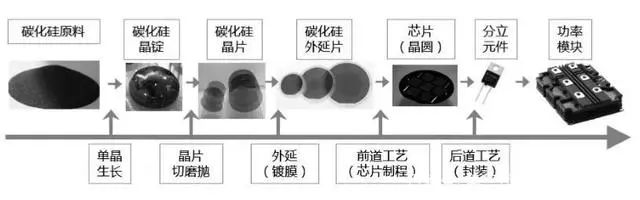
目前,SiC衬底主要制备过程大致分为两步:第一步SiC粉料在单晶炉中经过高温升华之后在单晶炉中形成SiC晶锭;第二步通过对SiC晶锭进行粗加工、切割、研磨、抛光,得到透明或半透明、无损伤层、低粗糙度的SiC晶片(即SiC衬底)。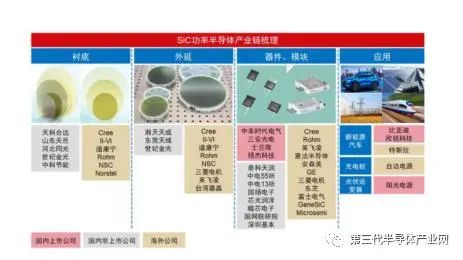
高技术门槛导致第三代半导体材料市场以日美欧寡头垄占,国内企业在SiC衬底方面以4英寸为主。目前,国内已经开发出了6英寸导电性SiC衬底和高纯半绝缘SiC衬底,山东天岳公司、北京天科合达公司和河北同光晶体公司分别与山东大学、中科院物理所和中科院半导体所进行技术合作与转化,在SiC单晶衬底技术上形成自主技术体系。国内目前已实现4英寸衬底的量产;同时山东天岳、天科合达、河北同光、中科节能均已完成6英寸衬底的研发;中电科装备已成功研制出6英寸半绝缘衬底。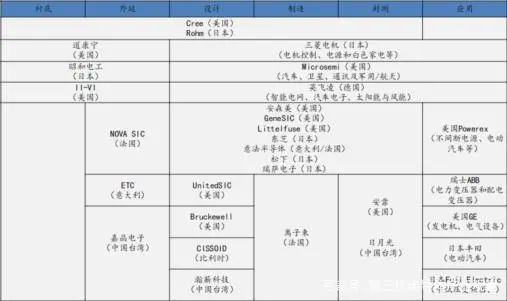
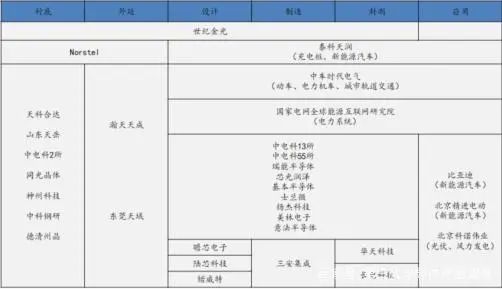
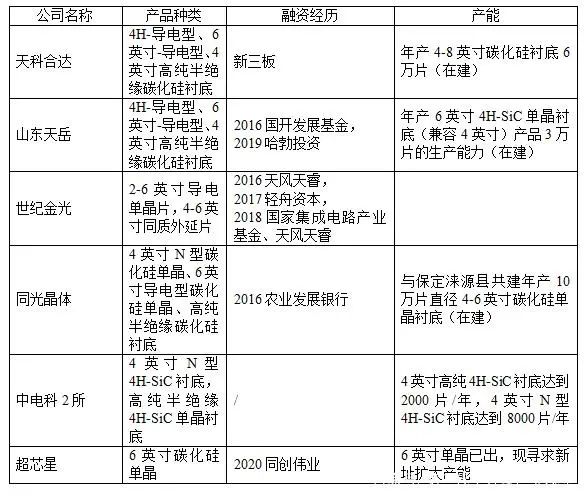
尽管全球碳化硅器件市场已经初具规模,但是碳化硅功率器件领域仍然存在一些诸多共性问题亟待突破,比如碳化硅单晶和外延材料价格居高不下、材料缺陷问题仍未完全解决、碳化硅器件制造工艺难度较高、高压碳化硅器件工艺不成熟、器件封装不能满足高频高温应用需求等,全球碳化硅技术和产业距离成熟尚有一定的差距,在一定程度上制约了碳化硅器件市场扩大的步伐。大尺寸碳化硅单晶衬底制备技术仍不成熟。目前国际上碳化硅芯片的制造已经从4英寸换代到6英寸,并已经开发出了8英寸碳化硅单晶样品,与先进的硅功率半导体器件相比,单晶衬底尺寸仍然偏小、缺陷水平仍然偏高。缺乏更高效的碳化硅单晶衬底加工技术。碳化硅单晶衬底材料线切割工艺存在材料损耗大、效率低等缺点,必须进一步开发大尺寸碳化硅晶体的切割工艺,提高加工效率。衬底表面加工质量的好坏直接决定了外延材料的表面缺陷密度,而大尺寸碳化硅衬底的研磨和抛光工艺仍不能满足要求,需要进一步开发研磨、抛光工艺参数,降低晶圆表面粗糙度。P型衬底技术的研发较为滞后。目前商业化的碳化硅产品是单极型器件。未来高压双极型器件需要P型衬底。目前碳化硅P型单晶衬底缺陷较高、电阻率较高,其基础科学问题尚未得到突破,技术开发滞后。近年来,我国碳化硅单晶材料领域取得了长足进步,但与国际水平相比仍存在一定的差距。除了以上共性问题以外,我国碳化硅单晶材料领域在以下两个方面存在巨大的风险:是本土碳化硅单晶企业无法为国内已经/即将投产的6英寸芯片工艺线提供高质量的6英寸单晶衬底材料。N型碳化硅外延生长技术有待进一步提高。目前外延材料生长过程中气流和温度控制等技术仍不完美,在6英寸碳化硅单晶衬底上生长高均匀性的外延材料技术仍有一定挑战,一定程度影响了中低压碳化硅芯片良率的提高。P型碳化硅外延技术仍不成熟。高压碳化硅功率器件是双极型器件,对P型重掺杂外延材料提出了要求,目前尚无满足需求的低缺陷、重掺杂的P型碳化硅外延材料。近年来我国碳化硅外延材料技术获得了长足进展,申请了一系列的专利,正在缩小与其它国家的差距,已经开始批量采用本土4英寸单晶衬底材料,产品已经打入国际市场。目前国内碳化硅外延材料产品以4英寸为主,由于受单晶衬底材料的局限,尚无法批量供货6英寸产品。碳化硅外延材料加工设备全部进口,将制约我国独立自主产业的发展壮大。虽然国际上碳化硅器件技术和产业化水平发展迅速,开始了小范围替代硅基二极管和IGBT的市场化进程,但是碳化硅功率器件的市场优势尚未完全形成,尚不能撼动目前硅功率半导体器件市场上的主体地位。国际碳化硅器件领域存在的问题主要有:碳化硅单晶及外延技术还不够完美,高质量的厚外延技术不成熟,这使得制造高压碳化硅器件非常困难,而外延层的缺陷密度又制约了碳化硅功率器件向大容量方向发展。碳化硅器件工艺技术水平还比较低,这是制约碳化硅功率器件发展和推广实现的技术瓶颈,特别是高温大剂量高能离子注入工艺、超高温退火工艺、深槽刻蚀工艺和高质量氧化层生长工艺尚不理想,使得碳化硅功率器件中存在不同程度的高温和长期工作条件下可靠性低的缺陷。在碳化硅功率器件的可靠性验证方面,其试验标准和评价方法基本沿用硅器件,尚未有专门针对碳化硅功率器件特点的可靠性试验标准和评价方法,导致试验情况与实际使用的可靠性有差距。在碳化硅功率器件测试方面,碳化硅器件测试设备、测试方法和测试标准基本沿用硅器件的测试方法,导致碳化硅器件动态特性、安全工作区等测试结果不够准确,缺乏统一的测试评价标准。除了以上共性问题外,我国碳化硅功率器件领域发展还存在研发时间短,技术储备不足,进行碳化硅功率器件研发的科研单位较少,研发团队的技术水平跟国外还有一定的差距等问题,特别是在以下三个方面差距巨大:在SiC MOSFET器件方面的研发进展缓慢,只有少数单位具备独立的研发能力,存在一定程度上依赖国际代工企业来制造芯片的弊病,容易受制于人,产业化水平不容乐观。碳化硅芯片主要的工艺设备基本上被国外公司所垄断,特别是高温离子注入设备、超高温退火设备和高质量氧化层生长设备等,国内大规模建立碳化硅工艺线所采用的关键设备基本需要进口。当前碳化硅功率模块主要有引线键合型和平面封装型两种。为了充分发挥碳化硅功率器件的高温、高频优势,必须不断降低功率模块的寄生电感、降低互连层热阻,并提高芯片在高温下的稳定运行能力。目前碳化硅功率模块存在的主要问题有:采用多芯片并联的碳化硅功率模块,由于结电容小、开关速度高,因此在开关过程中会出现极高的电流上升率(di/dt)和电压上升率(dv/dt),在这种情况下会产生较严重的电磁干扰和额外损耗,无法发挥碳化硅器件的优良性能。碳化硅功率模块的封装工艺和封装材料基本沿用了硅功率模块的成熟技术,在焊接、引线、基板、散热等方面的创新不足,功率模块杂散参数较大,可靠性不高。碳化硅功率高温封装技术发展滞后。目前碳化硅器件高温、高功率密度封装的工艺及材料尚不完全成熟。为了发挥碳化硅功率器件的高温优势,必须进一步研发先进烧结材料和工艺,在高温、高可靠封装材料及互连技术等方面实现整体突破。尽管碳化硅功率器件应用前景广阔,但是目前受限于价格过高等因素,迄今为止,市场规模并不大,应用范围并不广,主要集中于光伏、电源等领域。目前碳化硅器件应用存在的主要问题有:碳化硅功率器件的驱动技术尚不成熟。为了充分发挥碳化硅功率器件的高频、高温特性,要求其驱动芯片具有工作温度高、驱动电流大和可靠性高的特点。目前驱动芯片沿用硅器件的驱动技术,尚不能满足要求。碳化硅功率器件的保护技术尚不完善。碳化硅功率器件具有开关频率快、短路时间短等特点,目前器件保护技术尚不能满足需求。碳化硅器件的电路应用开关模型尚不能全面反映碳化硅功率器件的开关特性,尚不能对碳化硅器件的电路拓扑仿真设计提供准确的指导。碳化硅功率器件应用的电路拓扑尚不够优化。目前碳化硅功率器件的应用电路拓扑基本上沿用硅器件的电路拓扑,没有开发出完全发挥碳化硅功率器件优势的新型电路拓扑结构。整体而言,第三代半导体技术尚处于发展状态,还有许多不足之处。以当前运用程度最高的碳化硅为例,其技术上尚有几个缺陷:材料成本过高。目前碳化硅芯片的工艺不如硅成熟,主要为4英寸晶圆,材料的利用率不高,而Si芯片的晶圆早已经发展到12寸。具体而言,相同规格的产品,碳化硅器件的整体价格达到硅器件的5-6倍。高温损耗过大。碳化硅器件虽然能在高温下运行,但其在高温条件下产生的高功率损耗很大程度上限制了其应用,这是与器件开发之初的目的相违背的。封装技术滞后。目前碳化硅模块所使用的封状技术还是沿用硅模块的设计,其可靠性和寿命均无法满足其工作温度的要求。如上所述,碳化硅器件性能优势突出、应用场景明确、又有产业链上下游龙头企业积极投入,可目前市场渗透率仍低。究其原因,即为受制于高制造成本、低技术成熟度两大屏障。破此二障,是技术发展方向的核心。碳化硅器件制造的四个环节(衬底制作,外延制作、芯片制程、封装测试)各有发力。1)碳化硅器件制造成本高昂。目前碳化硅二极管、MOSFET的成本大概是同类硅产品的2-3倍、5-10倍,而下游客户认为大规模应用碳化硅器件的普遍价格区间应是同类硅器件1.5倍左右。成本高企的主要因素是原材料价格高,尤其是占标准碳化硅器件成本50%的衬底晶圆。碳化硅原材料的特性决定了高于硅晶圆的制备难度和成本。制备温度方面,碳化硅衬底需要在2500度高温设备下进行生产,而硅晶只需1500度;生产周期方面,碳化硅晶圆约需要7至10天,而硅晶棒只需要2天半;商业化晶圆尺寸方面,目前碳化硅晶圆主要是4英寸与6英寸,而用于功率器件的硅晶圆以8英寸为主,这意味着碳化硅单晶片所产芯片数量较少、碳化硅芯片制造成本较高。技术演进方向:衬底方面,国外龙头企业预计将在2022年左右开始批量生产8寸晶片;外延及器件方面,将继续提高产能及制造良品率。2)碳化硅产业发展时间不长,有待更多应用验证。碳化硅不像硅产业,已在几十年的研究中积累了一套很完整的数据。碳化硅的很多性能结论都是由硅的性质推导而来,不少特性数据有待进一步实证。此外,碳化硅功率器件的产品组合尚未完善。从整个功率半导体市场来看,功率器件种类多样,主要包括二极管、MOSFET、IGBT等,分别适用于不同的领域。但是目前,碳化硅器件市场还以二极管为主,MOSFET尚未大规模推广,IGBT仍在研发。碳化硅二极管主要用于替代硅二极管,结构复杂度较低,现已大规模商用化,2019年碳化硅二极管的碳化硅器件市场占比达到85%,可谓是目前最主要的碳化硅器件。碳化硅MOSFET可替代硅基IGBT,大规模应用仍受限于产品性能稳定性及器件成熟性。碳化硅IGBT尚在研发,预计将在5-10年后才能看到相关器件原型。技术演进方向:器件方面,正在发展3.3kv以上的高耐压器件、并引入沟槽式设计以提高器件性能和可靠性;封装方面,将优化封装工艺以发挥碳化硅耐高温优势。
*免责声明:今日半导体 转载仅为了传达一种不同的观点,不代表今日半导体对该观点赞同或支持,内容如有侵权,请联系本部删除!手机微信同15800497114。