随着社会的发展,工业的进步,工艺的精进,PCB产业发展的也是越来越好,工艺性能也是越来越精湛先进。不管是硬板还是软板还是软硬结合版,亦或是有散热性能好的陶瓷基板,都在告诉我们,创新无可限量!
目前来说,关于陶瓷基板比较成熟的有氧化铝陶瓷电路板、氮化铝陶瓷电路板,很多公司可以做3535、5050、7070等,富力天晟科技(武汉)有限公司可以接受客户定制,不管是什么规格都可以制作,但是一定要满足线间距大于20微米,更是采用全自动化的生产,无需过多的人力,也避免了很多流程上的失误。
这样一个重视科研技术和用户体验的朝阳企业,不仅为员工提供了相应的保障,也给客户带来了更全面,更成熟的用户体验,对于可能出现的溅铜脱落和气泡等问题,斯利通的工艺也是相当的成熟,一般线路板行业要求是结合力能达到18-30兆帕,而脱落是因为结合强度不够,我们产品的结合强度是45兆帕,即推力值和拉力值都是45兆帕,因而焊接后不会脱落。更是采用LAM激光活化技术,覆铜的厚度可根据客户的需求来做0.001-1mm,一般覆铜0.03mm,误差在+/-0.005mm,后期铜导电不会烧坏。此种产品主要存在于需要散热要求高的产品上,一般航天航空、汽车电子、照明、大功率电子元件上,让产品性能大化。
DPC薄膜工艺处于陶瓷PCB行业较高水平,可快速定制生产,满足客户需求。陶瓷基金属化基板拥有良好的热学和电学性能,是功率型LED封装、紫光、紫外的材料,特别适用于多芯片封装(MCM)和基板直接键合芯片(COB)等的封装结构,同时也可以作为其他大功率电力半导体模块的散热电路基板,大电流开关、继电器、通信行业的天线、滤波器、太阳能逆变器等。
陶瓷PCB行业预估在智慧照明市场有60亿美元的市值,并以每年增长7%的速度击败大多数“朝阳行业”,成为业内的新兴高科技企业,并在地铁,轨道交通,IGBT,新能源汽车等方面有广泛应用。
陶瓷基板市场前景广阔,富力天晟专注于生产高品质陶瓷基板,提升品牌影响力,着力于科研开发和高新科技应用,为您提供及时,贴心,的服务。
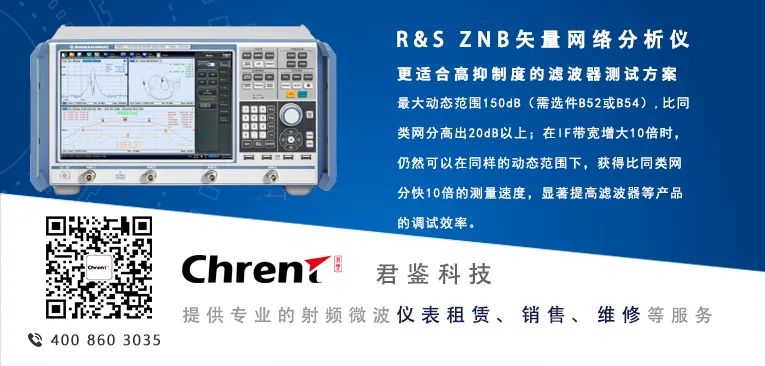
陶瓷基板又称陶瓷电路板,由陶瓷基片和布线金属层两部分组成。封装基板起着承上启下,连接内外散热通道的关键作用,同时兼有电互连和机械支撑等功能。陶瓷热导率高、耐热性好、机械强度高、热膨胀系数低,是功率半导体器件封装常用的基板材料。根据封装结构和应用要求,陶瓷基板可分为平面陶瓷基板和三维陶瓷基板两大类。
根据制备原理与工艺不同,平面陶瓷基板可分为薄膜陶瓷基板(TFC)、厚膜印刷陶瓷基板(TPC)、直接键合铜陶瓷基板(DBC)、活性金属焊接陶瓷基板(AMB)、直接电镀铜陶瓷基板(DPC)和激光活化金属陶瓷基板(LAM)等。
1.薄膜陶瓷基板(TFC)
TFC利用磁控溅射、真空蒸镀和电化学沉积等薄膜工艺在陶瓷基板表面形成金属层,然后通过掩膜和刻蚀等工艺形成特定的金属图形。该工艺工作温度低、布线精度高、金属层厚度可控以及金属陶瓷间结合强度高。常用于薄膜工艺的陶瓷基片材料主要有Al2O3、AlN 和 BeO等。薄膜陶瓷基板主要应用于电流小、尺寸小、散热要求高、布线精度要求高的器件封装。2.厚膜印刷陶瓷基板(TPC)
TPC采用丝网印刷工艺印刷金属布线层,制备工艺简单,对加工设备和环境要求低,具有生产效率高、制造成本低等优点。但由于丝网印刷工艺限制,TFC 基板无法获得高精度线路 ,此外,为了降低烧结温度,提高金属层与陶瓷基片结合强度,通常在金属浆料中添加少量玻璃相,这会不可避免地降低金属布线层的电导率和热导率。因此厚膜印刷陶瓷基板仅应用于对线路精度要求不高的电子器件封装,如汽车电子封装。3.直接键合铜陶瓷基板(DBC)
DBC陶瓷基板是在1000℃以上的高温条件下,在含氧的氮气中加热,使铜箔和陶瓷基板通过共晶键合的方式牢固结合在一起,其键合强度高且具有良好的导热性和热稳定性。广泛应用于绝缘双极二极管、激光器、聚焦光伏等器件封装散热中。4.活性金属焊接陶瓷基板(AMB)
AMB陶瓷基板是DBC工艺的进一步发展,该工艺通过含有少量稀土元素的焊料来实现陶瓷基板与铜箔的连接,其键合强度高、可靠性好。该工艺相较于DBC工艺键合温度低、易操作。制备工艺流程如下图。
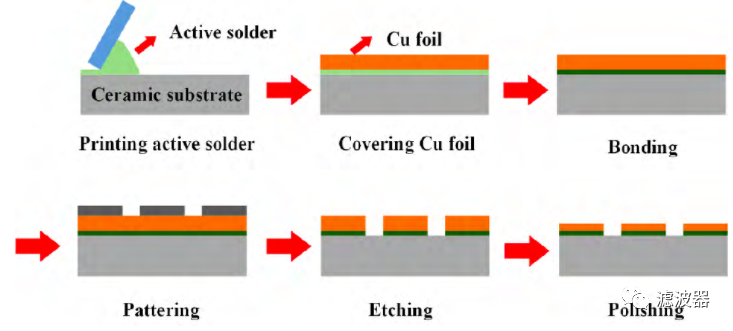
5.直接电镀铜陶瓷基板(DPC)
DPC陶瓷基板利用激光在陶瓷基片上打孔,采用半导体工艺在陶瓷基片上沉积Cu种子层,通过电镀工艺填孔,增厚金属层,该工艺具有电路精度高、制备温度低的特点。该工艺可实现陶瓷基板的垂直互连从而提高封装密度。缺点在于金属线路层采用电镀工艺制备,污染环境,电镀生长速度低,线路层厚度有限,难以满足大电流功率器件封装需求。DPC陶瓷基板主要应用于大功率LED封装。制备工艺流程如下图。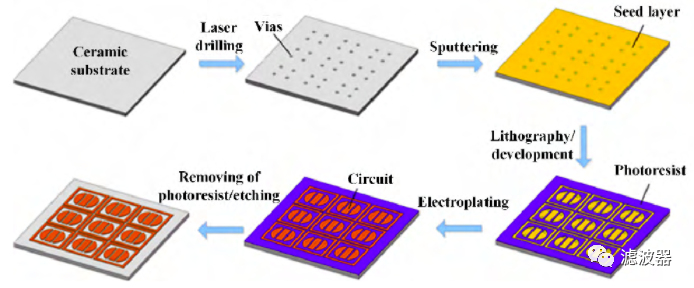
6.激光活化金属陶瓷基板(LAM)
LAM陶瓷基板通过激光束加热活化需要金属化的陶瓷基板表面,然后通过电镀或化学镀形成金属化布线。该工艺无需采用光刻、显影、刻蚀等微加工工艺,通过激光直写制备线路层,且线宽由激光光斑决定,精度高,可在三维结构陶瓷表面制备线路层,突破了传统平面陶瓷基板金属化的限制,金属层与陶瓷基片结合强度高,线路层表面平整,粗糙度在纳米级别。但其难以大批量生产,价格极高,目前主要应用于航空航天领域。常见的三维陶瓷基板主要有:高/低温共烧陶瓷基板(HTCC/LTCC) 、 多层烧结三维陶瓷基板(MSC)、直接粘接三维陶瓷基板(DAC)、多层镀铜三维陶瓷基板(MPC)以及直接成型三维陶瓷基板(DMC)等。
1.高温共烧陶瓷基板(HTCC)
HTCC基板制备过程中先将陶瓷粉(Al2O3或AlN)加入有机黏结剂,混合均匀成为膏状陶瓷浆料后,用刮刀将陶瓷浆料刮成片状,再通过干燥工艺使片状浆料形成生胚,然后根据线路层设计钻导通孔,采用丝网印刷金属浆料进行布线填孔,最后将生胚层叠加,置于高温炉中烧结。该工艺温度高,导电金属选择受限,只能采用熔点高但导电性较差的金属,制作成本较高。受限于丝网印刷工艺,线路精度较差,难以满足高精度封装需求。但HTCC基板具有较高机械强度和热导率,物化性能稳定,适合大功率及高温环境下器件封装。工艺流程如下图。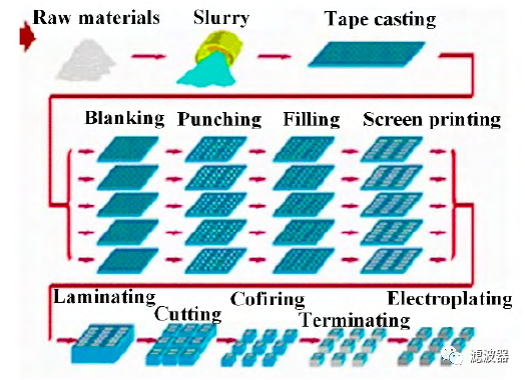
2.低温共烧陶瓷基板(LTCC)
与HTCC制备工艺类似,只是在陶瓷浆料中加入了一定量玻璃粉来降低烧结温度,同时使用导电性良好的Cu、Ag和Au等金属浆料,LTCC基板制备温度低,但生产效率高,可适应高温、高湿及大电流应用要求,在军工及航天电子器件中得到广泛应用。3.多层烧结三维陶瓷基板(MSC)
首先制备厚膜印刷陶瓷基板,随后通过多次丝网印刷将陶瓷浆料印刷于平面TPC基板上,形成腔体结构,再经高温烧结而成。MSC基板技术生产设备和工艺简单,平面基板与腔体结构独立烧结成型,腔体结构与平面基板均为无机陶瓷材料,热膨胀系数匹配,制备过程中不会出现脱层、翘曲等现象。缺点在于,下部TPC基板线路层与上部腔体结构均采用丝网印刷布线,图形精度较低,受丝网印刷工艺限制,所制备的MSC基板腔体厚度有限。因此MSC三维基板仅适用于体积较小、精度要求不高的电子器件封装。工艺流程如下图。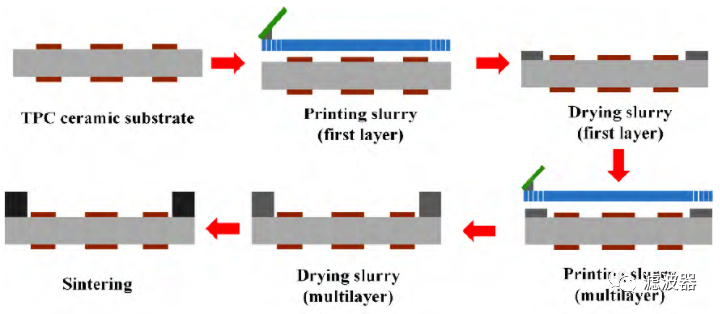
4.直接粘接三维陶瓷基板(DAC)
首先加工金属环和DPC陶瓷基板,然后采用有机粘胶将金属环与DPC基板对准后粘接、加热固化。工艺简单,成本低,可实现批量生产,所有制备工艺均在低温下进行,不会对DPC基板线路层造成损伤。但由于有机粘胶耐热性差,固化体与金属、陶瓷间热膨胀系数差较大,且为非气密性材料,目前DAC陶瓷基板主要应用于线路精度要求较高,但对耐热性、气密性、可靠性等要求较低的电子器件封装。采用无机胶替代有机胶的粘接,大大提高了DAC三维陶瓷基板的耐热性和可靠性。
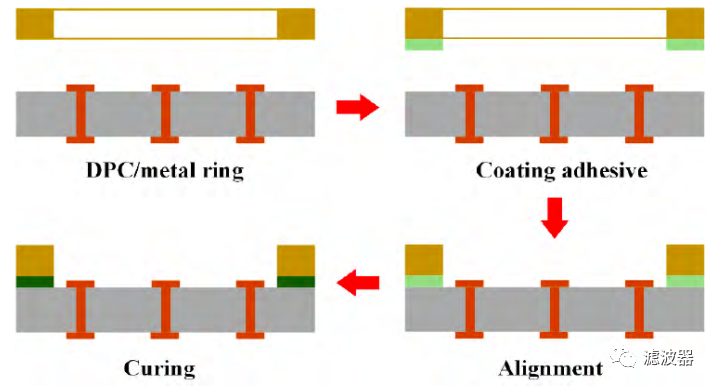
5.多层电镀三维陶瓷基板(MPC)
MPC基板采用图形电镀工艺制备线路层,避免基板线路粗糙问题,满足高精度封装要求。陶瓷基板与金属围坝一体化成型为密封腔体,结构紧凑,无中间粘结层,气密性高。MPC基板整体为全无机材料,具有良好的耐热性、抗腐蚀、抗辐射等。金属围坝结构形状可以任意设计,围坝顶部可制备出定位台阶,便于放置玻璃透镜或盖板。但干膜厚度限制,制备过程耗时长,生产成本高,由于电镀围坝铜层较厚,内部应力大,MPC基板容易翘曲变形,影响后续的芯片封装质量与效率。 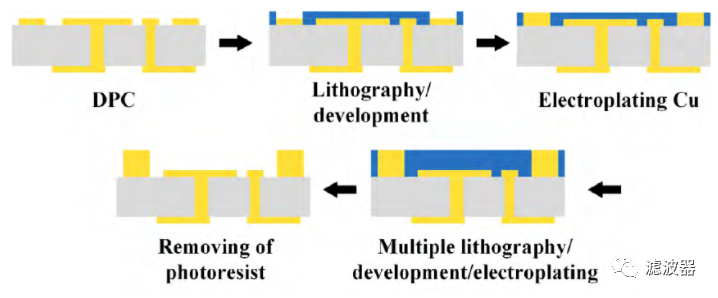
6.直接成型三维陶瓷基板(DMC)
首先制备平面DPC陶瓷基板,同时制备带孔橡胶模具,将橡胶模具与 DPC陶瓷基板对准合模后,向模具腔内填充牺牲模材料,待牺牲模材料固化后,取下橡胶模具,牺牲模粘接于DPC陶瓷基板上,并精确复制橡胶模具孔结构特征,作为铝硅酸盐浆料成型模具,随后将铝硅酸盐浆料涂覆于DPC陶瓷基板上并刮平,加热固化,最后将牺牲模材料腐蚀,得到含铝硅酸盐免烧陶瓷围坝的三维陶瓷基板。该工艺制备的三维陶瓷基板精度高,重复性好,适合量产。铝硅酸盐浆料加热后脱水缩合,主要产物为无机聚合物,其耐热性好,热膨胀系数与陶瓷基片匹配,具有良好的热稳定性。固化体与陶瓷、金属粘接强度高,制备的三维陶瓷基板可靠性高。围坝厚度(腔体高度)取决于模具厚度,理论上不受限制,可满足不同结构和尺寸的电子器件封装要求。 ●陶瓷基片材料Al2O3和AlN具有较好的综合性能,两者分别在低端和高端陶瓷基板市场占据主流。 ●平面陶瓷基板TFC基板主要应用于小电流光电器件封装;TPC基板主要应用于汽车传感器等领域;DBC和AMB基板主要应用于高功率、大温变的IGBT封装;DPC基板主要应用于大功率LED封装;而LAM基板应用于航空航天领域。 ●三维陶瓷基板制备技术HTCC/LTCC、MSC基板均采用丝网印刷与高温烧结工艺制备,腔体可靠性高,但金属线路层精度较差;MPC、DAC和 DMC基板通过在DPC基板上电镀、粘接和固化成型围坝,具有金属线路层精度高,围坝与基板结合强度高等优点,有望在今后的功率器件气密封装、三维封装与集成领域发挥重要作用。
1.陶瓷基板研究现状及新进展-陆琪、刘英坤、乔志壮、刘林杰、高岭2.电子封装陶瓷基板-程浩、陈明祥、罗小兵、彭洋、刘松坡
3. 先进陶瓷材料的6种后加工工艺
转自 中国粉体网 / 长安
目前市面上关于陶瓷材料的成型技术、烧结技术等方面研究较集中,而对后加工工艺研究偏少,本文则带你了解现有的陶瓷材料的后加工工艺。
陶瓷材料的后加工可根据陶瓷的形状、加工精度、表面粗糙度、加工效率和加工成本等因素选择不同的加工方法。常见的陶瓷加工方式主要有:机械加工、激光加工、超声波加工、磨料水射流加工、微波加工、电加工等方式。
机械加工方法主要有车削、钻削、铣削、磨削、研磨抛光等。
陶瓷材料车削一般选用金刚石或立方氮化硼刀具。由于陶瓷材料硬度和脆性非常大,车削加工难以保证其精度要求,并且影响加工效率,故车削加工应用不多,基本上还处于研究阶段。陶瓷材料钻削是使用直径很小的金刚石砂轮作为专用钻头,利用钻头端部磨粒的微切削作用从而实现材料的破坏去除。陶瓷材料铣削通常选用超硬刀如金刚石铣刀进行铣削的一种加工方法,在高频断续的切削力作用下使材料去除。然而,在铣削过程中,高频冲击力作用力容易导致加工表面发生脆断,振动则会导致瞬间去除深度的变化,降低表面质量。陶瓷材料的磨削加工是目前已有加工方法中应用最多的一种。利用金刚石磨针或砂轮与工件之间互相摩擦,使材料通过塑性变形、脆性断裂等方式去除。磨削加工中,切屑的清除是一大问题,一般采用冷却液清洗。冷却液不仅起到冲洗切屑粉末的作用,而且可以降低磨削区温度,提高磨削质量,减少磨粒周围粘结剂的热分解等。金刚石颗粒大小是影响陶瓷工件表面质量的又一主要原因,颗粒愈大,所加工表面粗糙度愈大,但加工效率愈高。在磨削加工陶瓷材料时,加工过程中受力不均易使裂纹产生。在工业生产的某些领域,仅靠磨削是达不到陶瓷件表面光洁度要求的,通常要采用研磨和抛光。陶瓷材料韧性小,脆性大,其强度很容易受表面裂痕的影响。加工表面愈粗糙,表面裂纹愈大,愈易产生应力集中,工件强度愈低。因此,研磨不仅是为了达到一定的粗糙度和高的形状精度,而且也是为了提高工件的强度。抛光是采用软质抛光器和细粉磨粒以较低的压力作用于工件的一种精加工过程。
随着陶瓷产品广泛应用,对产品规模化加工效率和成本控制提出了更高要求,针对陶瓷切割划线,一些常见的加工方式已经不能满足产品高效率、低成本发展的需求。激光作为一种非接触式的高能束精密加工技术,具有高效可控、热影响区小、无切削作用力、无刀具磨损,以及可加工高硬度、高脆性、高熔点等难加工材料的特点,受到越来越多的关注。
激光加工原理是利用高功率密度的均匀激光束作为热源,通过激光器光路整合聚焦在材料表面,使局部位置瞬时产生高温达到材料的熔化或气化温度,从而实现材料切割加工。缺点是激光加工过程中产生的大量热量易使工件表面形成裂纹与发生氧化。目前,对陶瓷激光加工主要有CO2激光器、光纤激光器、紫外激光器、皮秒激光器等。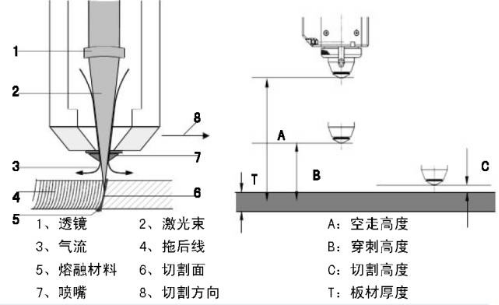
超声波加工是利用超声振动工具在有磨料的液体介质中或干磨料中产生磨料的冲击、抛磨、液压冲击及由此产生的气蚀作用来去除材料,或给工具或工件沿一定方向施加超声频振动进行振动加工,或利用超声振动使工件相互结合的加工方法。超声波加工技术应用于对陶瓷的铣削、打孔、磨削、车削、打磨等,可以有效解决陶瓷材料的加工难题,明显降低切削力与加工损伤,减少刀具磨损量,抑制脆性材料边缘破损,减少表面微裂纹的产生,提升工件的表面加工质量。然而,超声波加工的效率低,难以加工复杂曲面零件。
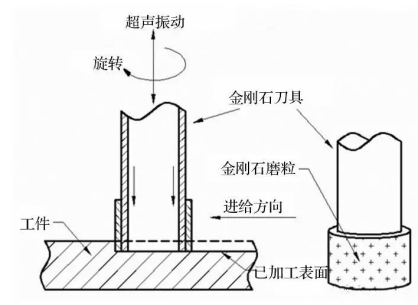
水射流通常是利用增压泵将水加压至一定压力,通过直径较小的喷嘴后喷射出来的高能束射流,它是一种加工能力强、加工范围广的冷态加工技术。纯水射流加工的水中无任何添加,仅利用纯水经高压形成的高速射流的动能作用在工件上,它的加工能力非常有限,对水的压力依赖程度高。到20世纪70年代,为了提高水射流的冲击力,人们开始在水中添加细小的固体颗粒,使射流束能量得到巨大的提升。这便是形成磨料水射流加工技术的开始。磨料水射流具有极强的破坏去除能力,加工工件的材料不受限制,如不锈钢、岩石、陶瓷、钛合金和高分子材料等。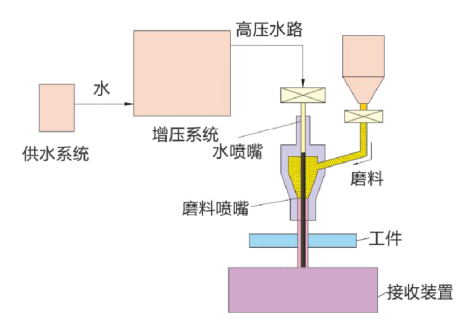
磨料水射流加工原理示意图(图片来源:郭露露.电解机械铣削Al2O3陶瓷材料技术研究)磨料水射流加工能力强、无热影响、无刀具磨损,且属于冷加工技术的范畴,在对材料的加工中,特别是在对各类难加工材料或热敏材料的加工中显示出了极大的优势,受到了制造业的广泛关注。经过多年的发展,磨料水射流技术面向不同加工需求逐渐形成了多种工艺方法,其中切割是磨料水射流技术应用最广泛和成熟的领域之一,然而,在磨料水射流切割后的工件上往往会出现拖尾、切口锥度等缺陷。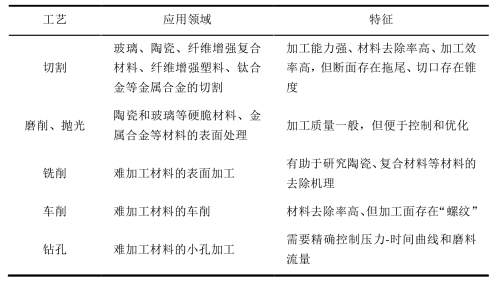
磨料水射流不同工艺方法的常见应用及特征(图片来源:王志敏.生物陶瓷磨料水射铣削表面质量研究)
微波加工的基本原理:当微波进入陶瓷内部后,陶瓷分子会吸收一部分微波,陶瓷分子在微波高频电场会相互摩擦,将振动的能量转换为热能量,从而去除材料。微波加工特点:穿透能力强,可以有效控制加工陶瓷微波。微波加工主要用在陶瓷的烧结、涂层、裂纹修复,也可以用来加工陶瓷孔。这种加工方法加工的陶瓷表面会出现灼烧情况,陶瓷表面粗糙度比较大。
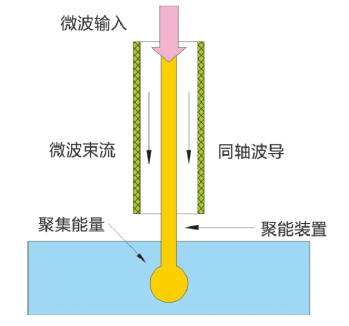
微波钻孔原理示意图(图片来源:郭露露.电解机械铣削Al2O3陶瓷材料技术研究)
电加工主要指电火花加工,对不导电的陶瓷材料来说,需借助辅助电极,将其置于陶瓷材料表面,辅助电极和工具电极之间留有一定间隙,两者之间能形成电火花放电,直至将辅助电极击穿,其上脱落的碎屑与从工作液中分解而出的碳在陶瓷表面形成新的导电层继续放电,陶瓷表面材料被去除。采用电火花加工技术可实现对复杂形状工件的加工,但由于其对被加工材料的强导电性能的要求,只有借助辅助电极才可实现对绝缘陶瓷的加工,且加工效率低、加工精度不高,在加工表面产生的高热量会导致其产生微裂纹,降低陶瓷的使役性能。1. 缪小进.磨料水射流切割机理及质量提升方法研究5. 郭露露.电解机械铣削Al2O3陶瓷材料技术研究
SAW声表滤波器与BAW滤波器技术
使用超过10年的基站天线之拆机详解
爱立信收购凯仕林天线和滤波器部门
滤波器专业英语初级篇(更新版)
国内首款BAW四工器产品下线
5G陶瓷介质滤波器逐步成为行业主流!
这25家滤波器公司都不知道,真是白活了
© 滤波器 微信公众号
